Butt Weld Symbols
Butt weld symbols provide crucial information about the joint design, welding processes, and other essential details necessary for successful welding operations. Understanding these symbols is essential for welders and professionals involved in fabrication, construction, and engineering industries.
In this article, I have covered the intricacies of butt weld symbols, their types along with their symbols with examples, unraveling their meaning, butt weld components, and it’s applications.
Whether you’re a seasoned welder looking to enhance your knowledge or a beginner eager to grasp the fundamentals, this comprehensive guide will equip you with the necessary insights to interpret and utilize butt weld symbols effectively.
What is a Butt Weld?
A butt weld is a type of weld where two pieces of metal are joined along their edges in a single plane.
“A butt weld is a type of welding joint used to join two pieces of metal (using fusion welding) or thermoplastic materials (using plastic welding) along their edges in a butt-to-butt configuration as shown in below examples.“
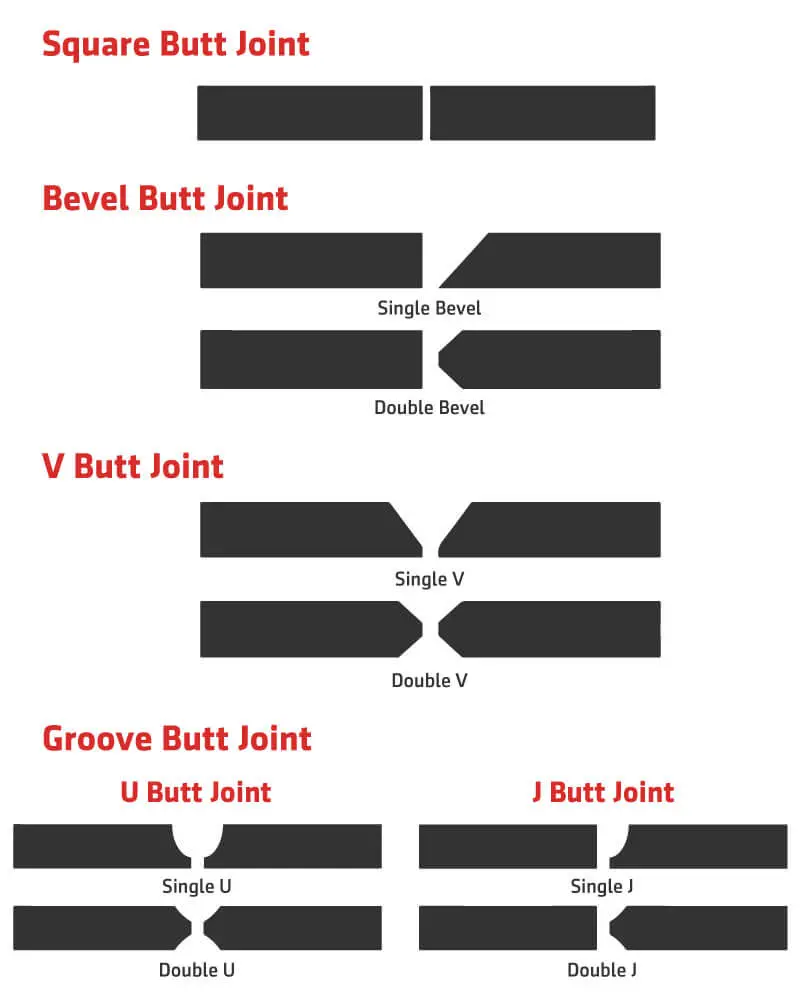
In a butt weld, the edges of the two materials to be joined are prepared by chamfering, beveling, or otherwise shaping them to create a V-shaped groove or a U-shaped groove. The groove allows for proper penetration of the filler material during the welding process.
Types of Butt Weld Joints
Below are the most common types of butt weld joints used for fabrication applications:
- Square Butt Joint
- Single V Butt Joint
- Double V Butt Joint
- Single U Butt Joint
- Double U Butt Joint
- Bevel Butt Joint
- J Butt Joint
- Flare V Butt Joint
Below I have explained each of above butt weld joint with examples.
Square Butt Joint
In a square butt joint, the two pieces of metal are joined together by aligning their edges in a square or right-angle configuration. There is no weld preparation for the weld faces in a square butt weld joint.
Below is the example of square groove without backing and with backing.
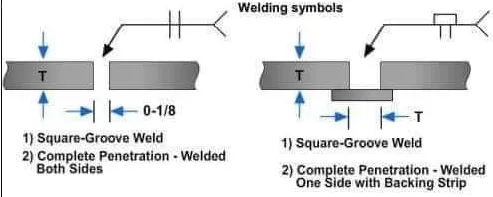
This type of joint is commonly used for welding plates or sheets together. For sheetmetal, square groove are most used as it is easy to fuse sheet metal. For higher thickness, square groove is used with high density energy processes such as laser welding or electron beam welding.
Single V Butt Joint
The single V butt joint involves preparing the edges of the two metal pieces by creating a V-shaped groove on one side. The other side remains flat. A weld bevel is prepared on both joining plates.
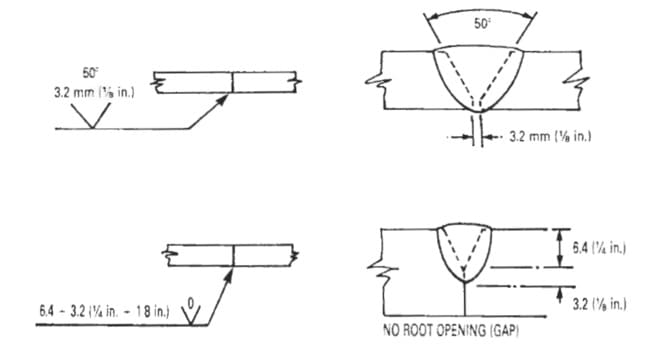
This joint is often used for thicker materials and provides good penetration and strength. V-groove is the most used butt weld type in the industry.
Double V Butt Joint
Similar to the single V butt joint, the double V butt joint involves creating V-shaped grooves on both sides of the metal pieces. Double V Butt weld joints are mainly used for welding thicker plates where access for both side welding is available.
Below is an example of double V-butt joint with its welding symbols. The groove is having a 60-Deg included angle and 1/8″ root gap.
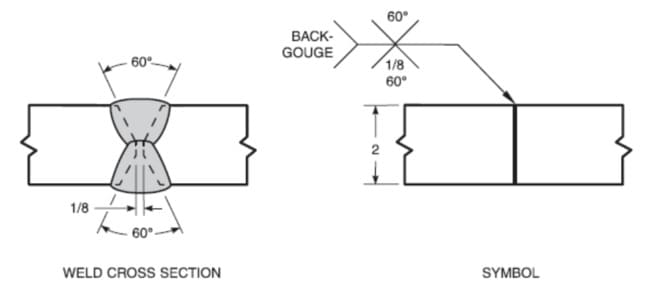
This joint offers increased strength and deeper penetration, making it suitable for thicker materials. Most of pressure vessels, reactors and other similar critical parts are welded using Double V butt weld joint.
Single U Butt Joint
The single U butt joint is formed by creating a U-shaped groove on one side of the metal pieces, while the other side remains flat.
Below is an example of Single U & Double Butt weld joint.
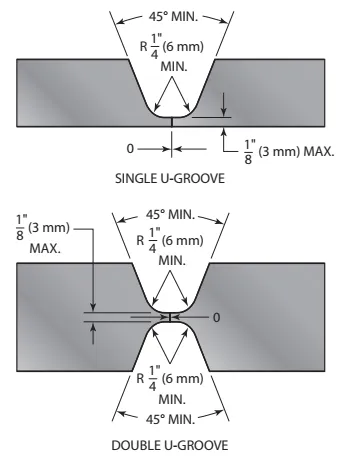
In below figure u can see the example of U- groove butt weld symbol. The size of U-groove is always shown on the left side of weld symbol. The included angle is shown inside the U butt weld symbol.
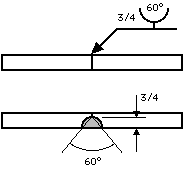
This joint is commonly used for medium thickness materials and provides good weld accessibility. Single U Butt weld groove are used where only side welding access is available. U preparation is costly as need to be prepare by machining.
Double U Butt Joint
The double U butt joint involves creating U-shaped grooves on both sides of the metal pieces. This joint offers increased strength and allows for deeper penetration, making it suitable for thicker materials.
An example of Double U butt weld is shown in earlier figure. The welding symbol of double U butt weld is similar to single U but it is shown for both side as shown in the below figure.
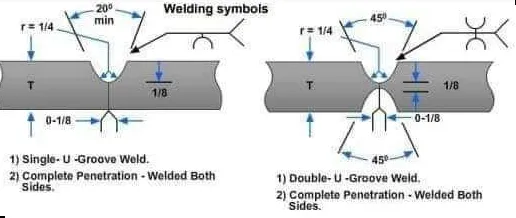
Bevel Butt Joint
In a bevel butt joint, the edges of the metal pieces are prepared by creating a beveled or angled surface on one only. Bevel butt weld have two types:
- Single Bevel Butt Weld &
- Double Bevel Butt weld.
The welding symbol for a bevel weld replicate its configuration and shown below:
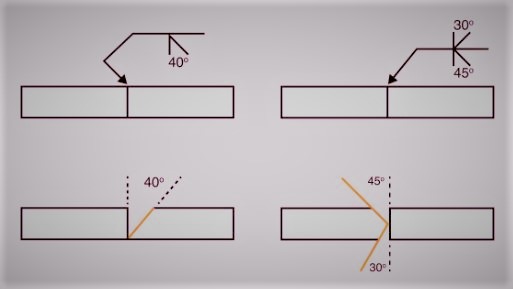
Bevel weld is a type of V groove but here only side of the plate is having slope made. This allow saving in welding consumables. Care must be taken to ensure full fusion between the members especially the one without weld bevel.
J Butt Joint
The J butt joint is formed by preparing one side of the metal pieces with a J-shaped groove, while the other side remains flat. Welding symbol for J Butt joint weld is shown below.
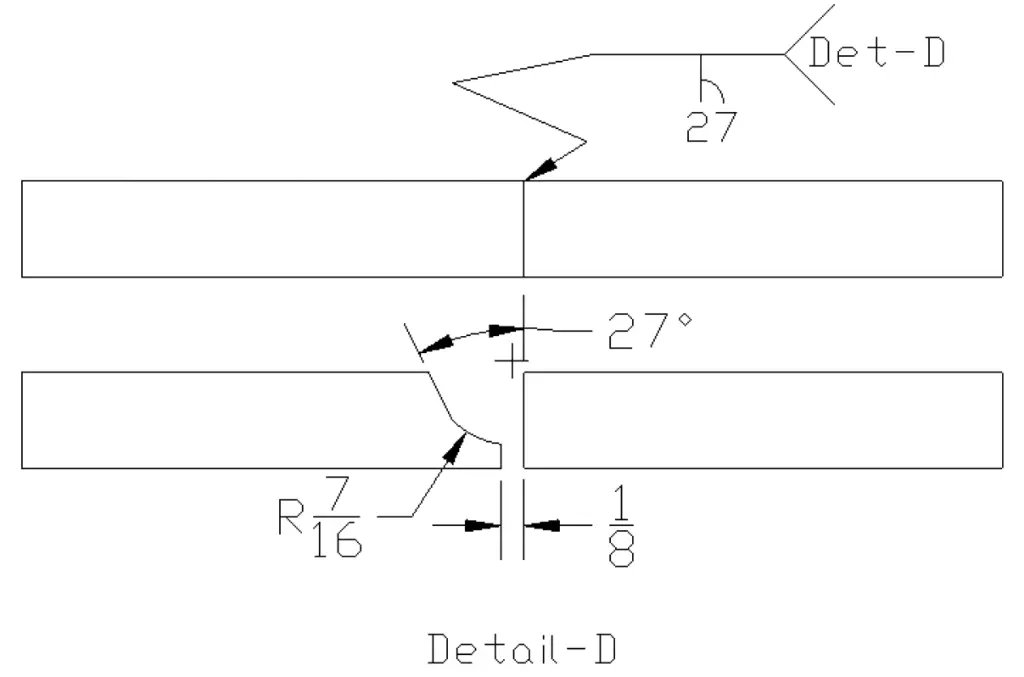
This joint is commonly used for thinner materials and provides good accessibility for welding.
Flare V Butt Joint
The flare V butt joint involves creating a V-shaped groove on both sides of the metal pieces, with the width of the groove wider on one side. Different types of flare welds and their respective weld symbols are shown below:
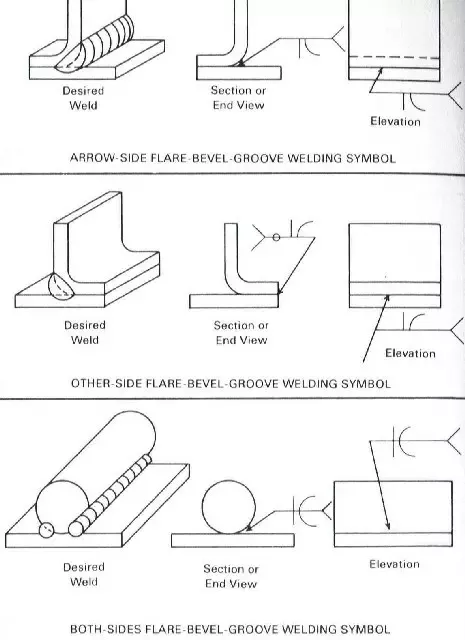
This joint is often used for thicker materials and provides increased weld strength and improved penetration.
Understanding the Butt Weld Symbol
The butt weld symbol specifically consists of:
- A arrow line.
- A reference line.
- A weld symbol according to the groove type.
- Tail for additional information if required.
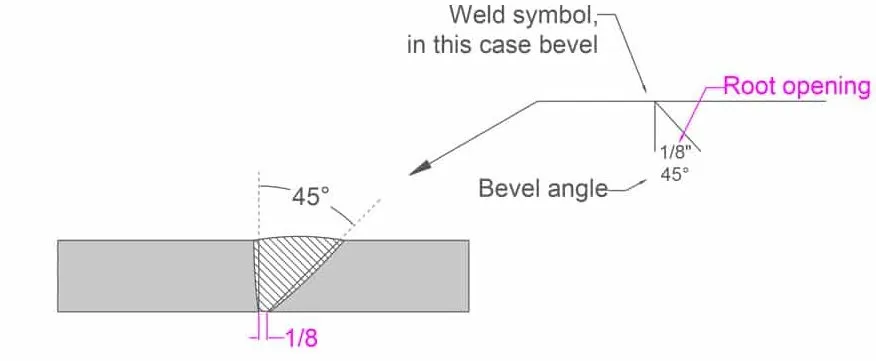
The reference line is the anchor of all welding symbols and is used to apply the necessary information.
The butt weld symbol typically appears as a shape representing the groove appearance such as V-U-J, etc. The symbol can be on the top or bottom of the reference line, indicating where the weld should be placed relative to the joint.
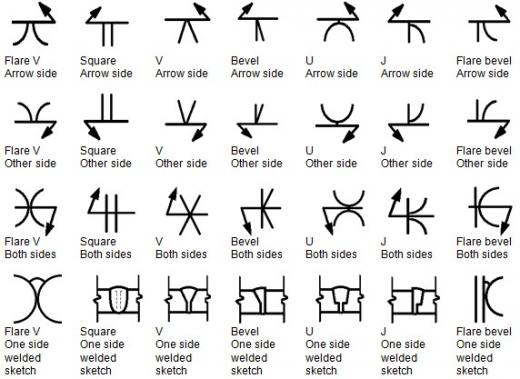
For example, if the symbol is above the reference line, the weld will be on the “arrow side,” and if it’s below, the weld will be on the “other side.” If the symbol is on both sides of the reference line, this denotes a double butt weld.
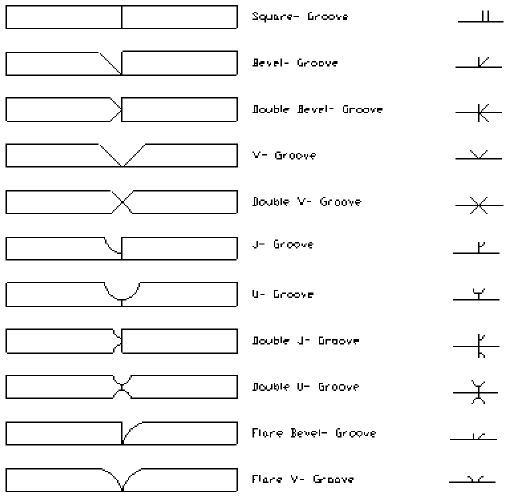
Advantages of Butt Weld
The Main Advantages of Butt Weld are:
- Strong joint
- Efficient and cost-effective
- Clean and aesthetically pleasing finish
- Suitable for high-pressure applications
- Minimal distortion
- No additional materials required
- Versatile and can be used with various materials
- Long-lasting and durable
- Provides excellent structural integrity
- Easy to inspect and test
Disadvantages of Butt Weld
The Main disadvantages of Butt Weld are:
- Limited joint thickness
- Requires skilled labor
- Time-consuming process
- High equipment and setup costs
- Susceptible to defects and imperfections
- Limited accessibility for welding in tight spaces
- Potential for distortion and warping
- Difficult to weld dissimilar metals
- Limited flexibility in joint design
- Requires proper alignment and fit-up