Whether you’re working on constructing bridges, buildings, or industrial structures, understanding double bevel welds is most commonly and essential welds for ensuring the structural integrity.
“A double bevel weld can be defined as a type of joint where two pieces of metal are joined together at an angle using a bevel-shaped groove on both sides of one joining member only.“
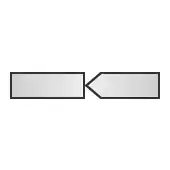
This groove is created by removing material from one piece on only one side before welding them together. The resulting joint created by the fusion between these two V-grooves provides exceptional strength and resistance to shear forces.
💥 The purpose behind utilizing double bevel welds stems from their ability to distribute stress more evenly across the joint. By preparing V-grooves on both sides of the workpieces and subsequently filling them with molten metal during welding, a larger surface area for welding is achieved compared to other types of joints like single or butt welds. Consequently, this leads to enhanced load-bearing capacity and superior performance under dynamic loading conditions. 💥
Now that we have established an overview of what double bevel welds are let us explore further how they differ from single bevel welds through symbol representation and application examples.
What is double bevel weld?
The double bevel weld is a type of joint configuration that involves welding two pieces of metal and only one is having the beveled edges before joining them together.
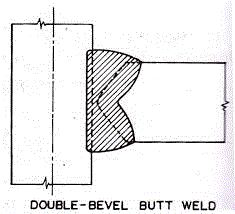
This welding technique creates a Half V-shaped groove on both sides of the metal, allowing for better penetration and stronger welds. Bevel weld is also known as HV weld in ISO standards such as EN15085-3.
The double bevel weld is commonly used in industries where high strength and integrity are crucial, such as in structural steel fabrication and pipeline construction.
Understanding the double bevel weld symbol
The symbol used to represent a double bevel weld consists of three components:
- Arrow line
- Reference line
- Bevel weld symbol
- Tail (optional)
The main primary weld symbol for a double bevel Groove weld is shown below:
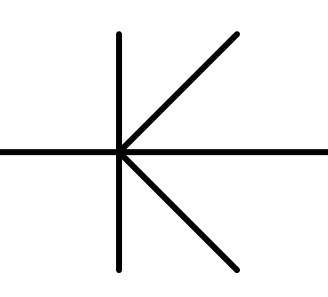
Each Half V-groove represents one half of the joint, indicating that both sides will require welding. The straight line connecting the V-grooves indicates that there should not be any gap between them.
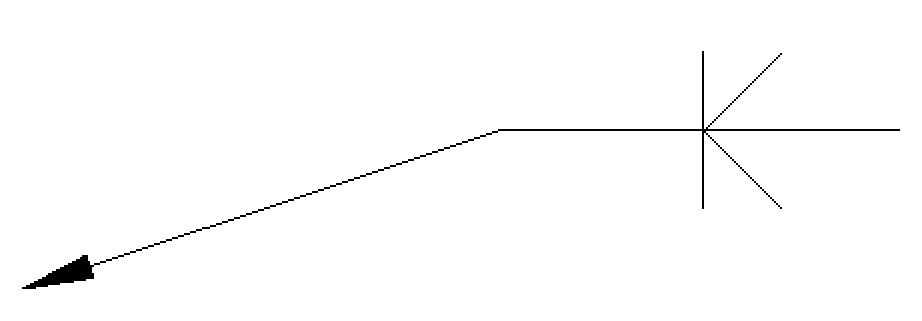
This symbol holds significant importance during welding procedures as it provides clear instructions for fabricators and welders. It helps communicate crucial information such as groove angles, root openings, and type of weld preparation required for each side of the joint.
By referencing this symbol in their blueprints or drawings, engineers can ensure that precise specifications are followed during fabrication to achieve strong and structurally sound joints.
For example, consider a project involving the construction of an I-beam column connection using double bevel welds. The blueprint would include symbols representing double bevel joints where each side requires a certain angle for bevelling (e.g., 30 degrees) and specific root opening dimensions (e.g., 1/4 inch).
These details are vital for achieving accurate fit-up during assembly and ensuring proper penetration while welding. Therefore, understanding the meaning behind the double bevel weld symbol is essential for accurately interpreting engineering designs and performing successful welding operations.
Comparative Analysis between Single Bevel and Double Bevel Welds
Single bevel welds, also known as single V-groove welds, are a type of joint where the edges of one piece of metal is chamfered or sloped on one side to form a groove weld as shown in below example.
The welding is then performed on this V-shaped groove, allowing for the fusion and joining of the two pieces. This type of weld joint is commonly used in situations where there is limited access from only one side.
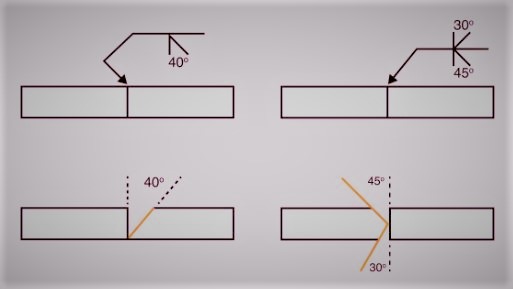
One advantage of single bevel welds is that they require less material removal compared to double bevel welds. This makes them more cost-effective and time-efficient since less preparation work is needed before the actual welding process can begin. Additionally, single bevel joints provide better control over penetration depth during welding, making it easier to achieve desired weld quality.
However, there are some disadvantages to using single bevel welds. Firstly, they tend to have weaker resistance against bending forces compared to double bevel joints due to their unilateral nature. Moreover, achieving proper root penetration can sometimes be challenging with a single-sided access approach.
On the other hand, double bevel welds involve chamfering both sides of the metal piece at an angle so that when they are joined together, they form a V shape similar to single beveled joints but with an additional groove on one side or both sides depending upon requirements.
Typically, this type requires more preparatory work than single-beveled ones. Despite this drawback, double-beveled seams have several advantages. One significant benefit lies in their increased strength which enables them resist higher bending forces.
A skew angles allow greater accessibility while providing room for deeper penetration. Once properly executed, a double-beveled seam offers improved overall structural integrity. Compared to negatives associated with single beveled joints, diamond-pattern grooves offer favorable versatility.
Furthermore, welders generally find it easier yet essential in certain industries to produce high quality double bevel welds due to upper-hand in control they offer over penetration depth.
Key considerations when using a double bevel joint
Proper preparation and fit-up requirements are crucial when dealing with double bevel joints. The preparation involves carefully removing any surface contaminants, such as rust or paint, from the surfaces to be welded. It is also important to accurately measure and mark out the dimensions of the joint according to the welding specifications.
Fit-up requirements involve aligning the two pieces of material that will be joined together in a precise manner. This ensures that when the weld is applied, it creates a strong and secure bond between the two components. Achieving proper fit-up can sometimes pose challenges due to various factors such as tolerance discrepancies between materials or structural distortions arising during fabrication.
Challenges encountered with double bevel joints often stem from their complexity compared to simpler joint types. One common challenge is maintaining uniformity throughout the entire weld length, especially on thicker materials where heat dissipation can vary significantly. Proper coordination of welding parameters like travel speed, arc voltage, and wire feed rate becomes crucial for achieving consistent quality throughout.
Another challenge can arise from distortion during welding caused by internal stress within complex-shaped members being joined together through a double bevel joint configuration. This requires careful planning and consideration of pre-heat techniques or post-weld treatments such as stress relieving methods.
By paying close attention to these considerations and addressing potential challenges proactively, welders can ensure successful execution of a strong and reliable double bevel joint.
Differences in Joint Design Parameters Between Single vs. Double Bevel Welds
When it comes to welding, the joint design plays a crucial role in determining the strength and durability of the final weldment. This is why understanding the differences between various joint designs, such as single and double bevel welds, is essential.
One significant difference between single and double bevel welds lies in their joint preparation. In a single bevel weld, only one side of each member is prepared with a beveled edge before welding. On the other hand, a double bevel weld requires both sides of each member to have a beveled edge. This means that for double bevel joints, not just one but two edges need to be prepared accurately for proper fitting during assembly.
Furthermore, another key parameter that sets these two types of joints apart is the included angle formed by the meeting point of two members after preparation. In single bevel welds, there will typically only be one included angle present at this point since only one side has been prepared with a sloping edge. However, in double bevel joints where both members are prepared with sloping edges on opposing sides from opposite directions, two included angles will form when they meet.
Understanding these differences between single and double bevel welds allows fabricators and engineers to select an appropriate joint design based on factors like material thicknesses being joined or application requirements for increased strength or aesthetics.
The Significance of Double Bevel Welds
Double bevel welds are widely used in various welding applications due to the benefits they offer. One of the main advantages is increased strength and structural integrity. By welding from both sides of the joint, double bevel welds create a more secure fusion between metal components, providing greater resistance to bending or twisting forces.
Furthermore, double bevel welds allow for better control over penetration depth. This means that the welder can ensure that the entire thickness of material is properly fused, reducing any potential weak spots or defects. The symmetrical nature of double bevel welds also minimizes distortion during cooling, resulting in a more aesthetically pleasing and structurally sound finished product.
Another advantage is that double bevel weld joints distribute stress more evenly across the welded area compared to single bevel joints. This helps prevent localized stress concentration points that could lead to failure under load conditions. In situations where high strength and durability are paramount, such as in construction or heavy machinery applications, using a double bevel joint can greatly enhance overall performance and reliability.
Double Bevel Weld Meaning?
Double bevel welding is an intriguing type of welding joint that involves the creation of a bevel on both sides of one joining member. This approach offers unique advantages, such as increased strength and better penetration, making it a highly sought-after method in various industries.
The process requires precision and skill, as the angles of the bevels need to be carefully calculated to ensure a proper fit and secure bond.