Butt welding is a widely used welding technique that plays a crucial role in joining metal components in various industries.
Whether in construction, manufacturing, or fabrication, understanding the different aspects of butt welding is essential for creating strong and reliable welds. In this article, we will explore the types of butt welds, their sizes, and the factors that influence their strength.
What is a Butt Weld Joint?
A butt weld joint is a commonly used welding joint where two metal pieces are joined together along their edges in a butt-to-butt configuration. In this type of joint, the edges of the metal pieces are aligned and brought into contact, creating a seam that is then welded to form a strong and continuous bond.
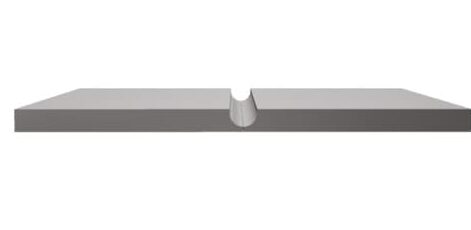
Types of Butt Welds
The main types of Butt Welds are:
- Square butt weld,
- Single V butt weld,
- Single bevel & double bevel butt weld
- Double V butt weld
- J-butt weld
- U Butt weld.
Square Butt Weld: This type of butt weld is formed when two metal pieces with square-cut ends are joined along a straight line. It is commonly used when the joint does not require any additional reinforcement or when the materials being joined have sufficient thickness.
Single V Butt Weld: In a single V butt weld, a V-shaped groove is created by removing material from one or both of the metal pieces. The V groove allows for a larger weld area and deeper penetration, resulting in increased strength and better fusion.
Double V Butt Weld: Similar to the single V butt weld, the double V butt weld involves creating two V-shaped grooves, one on each metal piece. This type of weld provides increased strength and improved fusion as it allows for a larger weld area and deeper penetration from both sides.
J Butt Weld: In a J butt weld, one metal piece is shaped like the letter “J,” with a curved edge, while the other piece is flat. The curved edge of the J-shaped piece fits snugly against the flat surface, creating a joint that is easy to align and weld.
Butt Weld Size
The size of a butt weld refers to the dimensions of the weld joint. It is determined by factors such as the thickness of the metal pieces being joined and the welding specifications. Weld size is typically specified in terms of its leg length, throat thickness, or penetration depth.
Throat Length: throat length in a butt weld refers to the distance from the root of the weld joint to the outer surface of the weld. It is an important measurement as it affects the overall strength and load-bearing capacity of the weld.
Throat Thickness: Throat thickness is the minimum distance from the root of the weld joint to the face of the weld. It is a critical dimension that determines the strength of the weld.
Butt Weld Strength
The strength of a butt weld depends on several factors, including the welding technique, filler material, weld joint design, and proper execution. A well-executed butt weld ensures proper fusion between the base metals and the filler material (if used), resulting in a weld joint with high strength and integrity.
To maximize butt weld strength, it is essential to ensure proper joint preparation, including cleaning and beveling the edges, maintaining the correct welding parameters, and using the appropriate welding technique for the specific materials being joined. Additionally, selecting the right filler material that matches or exceeds the base metal’s strength will contribute to the overall strength of the weld.
Butt Weld vs Fillet Weld
Aspect | Butt Weld | Fillet Weld |
---|---|---|
Joint Configuration | Two metal pieces are joined along their edges in a butt-to-butt configuration. | Two metal pieces are joined at a right angle, creating a triangular fillet between them. |
Joint Strength | Generally stronger as it provides a larger surface area for welding and more direct load transfer. | Strength depends on the size and throat thickness of the fillet. It is typically not as strong as a butt weld. |
Welding Technique | Can involve various welding techniques such as arc welding, MIG welding, or TIG welding. | Usually created using arc welding techniques like shielded metal arc welding (SMAW) or gas metal arc welding (GMAW). |
Joint Preparation | Requires edge preparation, including cleaning, beveling, or chamfering, to ensure proper alignment and fusion. | Typically requires less joint preparation compared to a butt weld. |
Welding Position | Can be performed in various positions: flat, horizontal, vertical, or overhead, depending on the welding technique and job requirements. | Commonly performed in the flat or horizontal position, but can also be done in other positions. |
Application | Commonly used for joining metal plates or sheets in a linear manner. | Suitable for joining two metal pieces at right angles, reinforcing lap joints, or adding strength to a corner joint. |
Appearance | The weld is typically flush or slightly recessed between the metal pieces. | Creates a visible triangular fillet that extends along the joint. |
Weld Volume | Typically requires more welding material and time due to the larger surface area and joint length. | Requires less welding material and time compared to a butt weld. |
Weld Accessibility | May require access to both sides of the joint for proper welding and complete fusion. | Can often be performed from one side, making it more accessible and easier to execute. |