Weld Surfacing or Weld Overlay Welding
Weld surfacing, also known as weld overlay, is a process of depositing one or more layers of material onto a base metal to improve its surface properties. This technique is commonly used to enhance the corrosion resistance, wear resistance, or mechanical properties of various metal components.
In this article, we’ll explore the welding symbols associated with weld surfacing, as defined by the American Welding Society (AWS) and the International Organization for Standardization (ISO), and discuss their applications in various industries.
What is Weld Surfacing or Weld Overlay?
Weld surfacing is a welding technique where a thin layer of material, usually a corrosion-resistant or wear-resistant alloy, is deposited onto the surface of a base metal. The purpose of this process is to improve the performance or extend the service life of metal components that are subjected to harsh operating conditions, such as high temperatures, corrosive environments, or abrasive wear.
There are several methods of weld surfacing, including:
- Gas metal arc welding (GMAW)
- Gas tungsten arc welding (GTAW)
- Submerged arc welding (SAW)
- Plasma transferred arc welding (PTAW)
Each method has its own advantages and limitations, with the choice of method depending on factors such as the material being used, the desired properties of the overlay, and the specific application.
AWS Weld Surfacing Welding Symbol
The American Welding Society (AWS) has established a standard set of welding symbols to ensure clear communication between designers, engineers, and welders. The AWS weld surfacing welding symbol consists of two half-circles attached to the reference line.
The height of surfacing weld/ weld overlay is always given on the left side of the weld symbol as shown in below example. The length of weld if required shall be mentioned on the right side of the weld symbol.
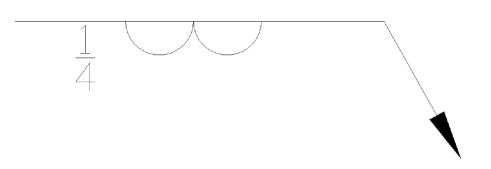
Surfacing welds can be created using single or multiple passes on components for various purposes, such as restoring worn materials, hardfacing a component, or enlarging part dimensions. This symbol is typically found only on the arrow side of a joint, and it is crucial for the arrow to accurately indicate the location where the surfacing will be applied.
In surfacing welds, it may be necessary to specify different sizes for the initial layer of buildup and subsequent layers. If there is a change in direction, this information might be displayed in the tail of a multi-reference welding symbol. A surfacing weld generally spans the entire length of the component, unless a dimension, note, or other indication states otherwise.
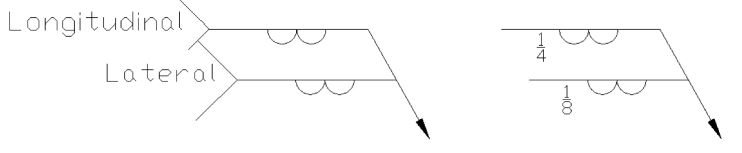
This consideration is also important when welding a shaft or another round object. For round objects, you may see axial (the length of the shaft) or circumferential (around the shaft) dimensions instead of longitudinal (long dimension) or lateral (short dimension). When welding a shaft or other round part, it is crucial to specify this information to avoid applying an incorrect procedure.
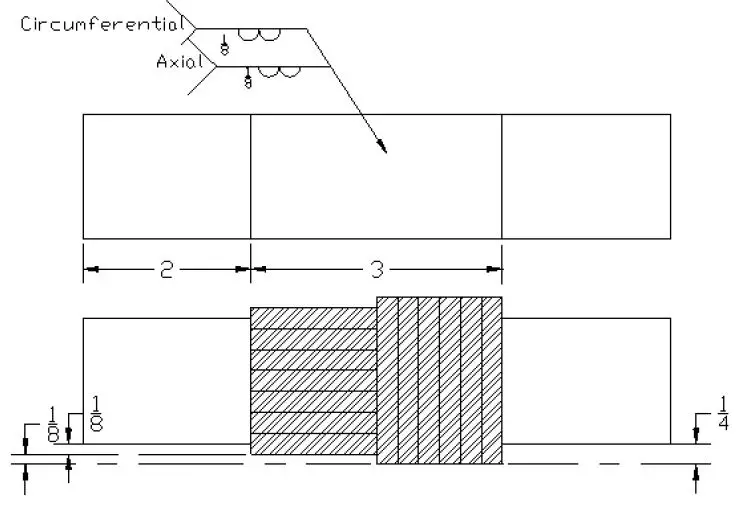
ISO Weld Overlay Welding Symbol
The International Organization for Standardization (ISO) has its own set of welding symbols, which are used mainly in Europe and other parts of the world. The ISO weld overlay welding symbol is similar to the AWS symbol, with a few differences such as It call Weld overlay instead of Surfacing weld.
Other than this the ISO welding symbol for Weld overlay is similar to the AWS surfacing weld symbol and follow same requirements for size.

Applications of Weld Surfacing
Weld surfacing has a wide range of applications across various industries, including:
- Oil and Gas: Weld overlay is used to protect components such as valves, pipes, and fittings from corrosion and wear in harsh environments.
- Power Generation: Turbine components, boiler tubes, and other parts in power plants can be surfaced to improve their resistance to high temperatures, erosion, and corrosion.
- Mining: Equipment used in mining, such as buckets, shovels, and crushers, can benefit from weld surfacing to increase their wear resistance and extend their service life without performing heat treatment.
- Chemical Processing: Chemical processing equipment, such as reactors, heat exchangers, and pumps, can be surfaced to protect against corrosion and wear caused by corrosive chemicals.
- Transportation: Components in the automotive, aerospace, and rail industries can be surfaced for improved wear resistance and to reduce friction.