The staggered stitch weld symbol is a graphical representation used in welding drawings to indicate the requirement for staggered stitch welds.
A staggered stitch weld is a type of intermittent weld where individual welds are placed intermittently along the length of the joint, alternating between the two sides.
What is a Staggered stitch weld?
A staggered stitch weld is a type of intermittent weld used in welding applications. It involves creating a series of individual weld stitches along the length of a joint, alternating between the two sides.
Instead of one continuous weld, the welder creates a pattern of intermittent welds with gaps between them.
The purpose of a staggered stitch weld is to provide localized reinforcement and strength to the joint while minimizing the heat input and potential distortion.
By alternating the welds on each side of the joint, it helps distribute the stress and heat generated during welding more evenly.
Staggered stitch weld symbol
A Staggered stitch weld symbol is similar to a double side fillet weld, the only difference is the placement of weld symbol on the reference line by shifting away from each other as shown in the below example.
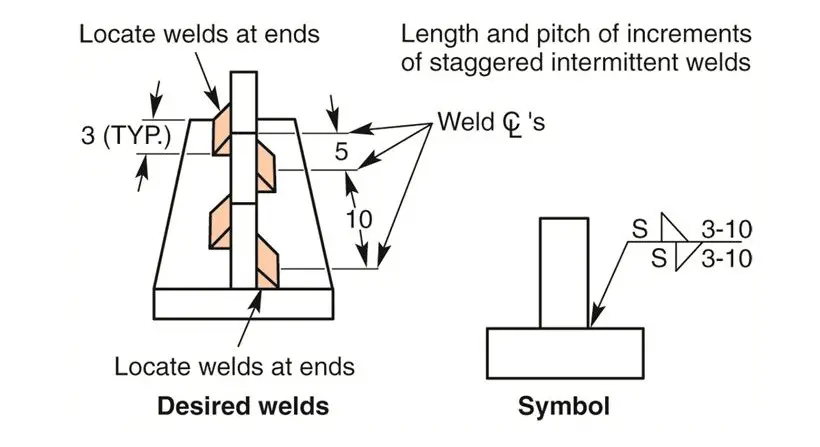
Below is an example of Chain intermittent and staggered stitch weld symbols as per AWS A2.4 Standards.
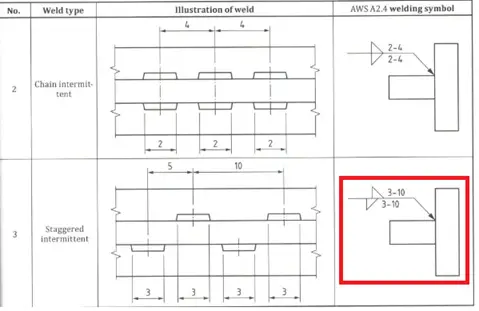
When would you use a staggered weld?
Staggered welding, also known as stitch welding, is employed in situations where full or seal welding would generate excessive heat and result in harmful distortion.
However, it is important to note that some stitch welds are placed due to inadequate project planning by the designer.
Stitch welding can pose corrosion issues, particularly crevice corrosion, due to the proximity of unwelded sections.
Controlling distortion can be achieved through various methods, not limited to stitch welding alone.
Ultimately, the primary reason for utilizing stitch welding is its time and resource efficiency, which can result in cost savings.
Advantages of Staggered stitch weld
Staggered stitch welds offer the following advantages:
- Reduced heat input, minimizing distortion.
- Controlled weld size for precise specifications.
- Improved weld strength and load distribution.
- Faster welding time, increasing productivity.
- Enhanced weld quality with fewer defects.
- Versatility for various joint configurations and materials.