👉Skip welding involves intentionally leaving gaps or spaces between welded sections rather than continuously joining them.👈 This technique helps distribute heat stress more evenly across a joint and reduces distortion in the metal.
👌🏻These symbols help communicate critical information about the spacing, size, and location of each skipped section within a joint assembly. 👌🏻
“In this article, we will explore skip welding from every angle – defining what it is exactly, discussing different types of skip welds including backstep and intermittent variations, comparing them with stitch welds for better differentiation, examining AWS (American Welding Society) standards for these particular symbols and finally demonstrating how to correctly show them on technical drawings using examples.“
⭐ So if you’re ready to dive into the world of skip weld symbols – their definition, types, and application – prepare yourself for an immersive journey that will enhance your understanding of this specialized aspect of welding fabrication techniques! ⭐
What is a skip weld?
🛑 The skip weld is a welding technique that involves creating intermittent, non-continuous welds along a joint or seam. These intermittent welds are strategically placed at specific intervals, leaving gaps between the welded sections.
🛑 This method is often used in structural and fabrication applications where continuous welding may not be practical or necessary.
🛑 One key advantage of skip welding is the reduction of distortion and stress on the welded components, as it allows for better control over heat input and minimizes warping.
🛑 Additionally, this technique can save time and material by eliminating the need for continuous long runs of welding. However, it requires careful planning to ensure that the intermittent welds still provide sufficient strength and durability to withstand intended loads or stresses.
Defining Skip Weld Symbol
To communicate the use of skip welds on engineering drawings, a specific symbol known as the skip weld symbol is used. This symbol helps indicate where and how skip welding should be implemented during fabrication.
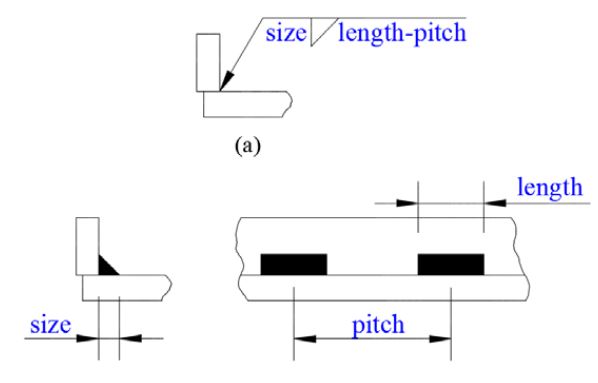
🌟 The skip weld symbol consists of a main weld symbol (e.g., fillet weld symbol as shown in below example), and length & pitch of skip weld stated on the weld symbol right side- short gaps or spaces at regular intervals. 🌟
These gaps indicate the areas where welding is not required and allows for reduced heat input and minimized distortion in the welded structure.
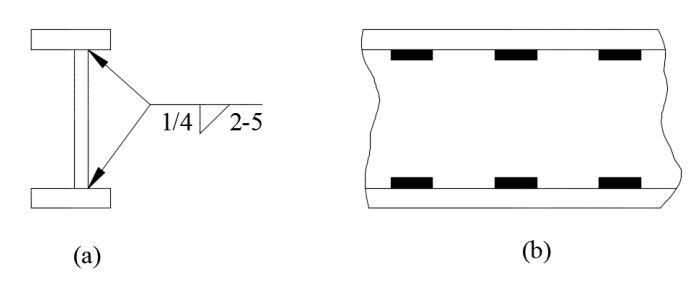
By using this symbol, designers can clearly convey their intent for determining which portions of a joint need to be welded using skip welds.
It’s important to note that the placement of the skip weld symbols in relation to other welding symbols within an overall welding symbol is significant. The location of these symbols provides valuable information about how skip welding should be carried out in conjunction with stitch or continuous welding methods.
Backstep Skip Weld vs Intermittent Skip Weld: A Comparison
When it comes to skip welds, there are two primary types that are commonly used :
- – backstep skip welds and
- intermittent skip welds.
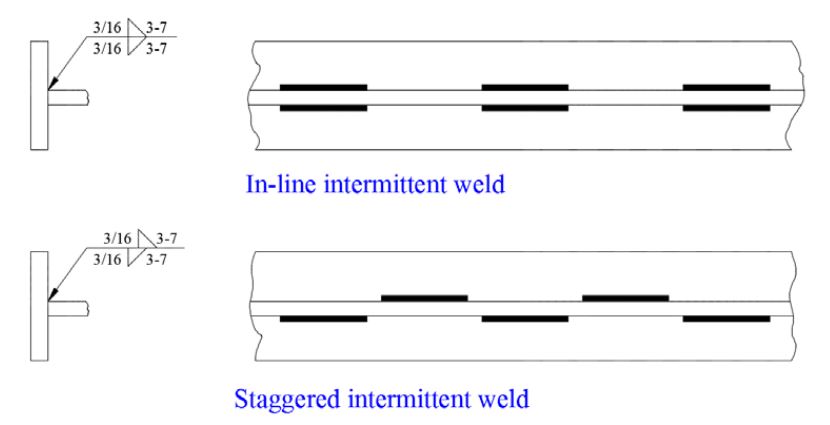
While they may seem similar at first glance, there are some key differences between the two.
🌟Backstep skip welds involve welding a series of short strokes or beads in a reverse order from the direction of progression. This means that each new bead starts slightly behind where the previous one ended. The purpose of this technique is to distribute heat evenly and reduce distortion in the metal being welded.
🌟On the other hand, intermittent skip welds involve welding separate sections or intervals with gaps in-between. Unlike backstep skip welds, which require continuous contact with the parent material, intermittent skip weld allows for breaks without compromising structural integrity. This type of skipping pattern is often used for aesthetic reasons or when joining materials with significant thickness variation.
To better understand these concepts, let’s consider an example:
🌟🌟 imagine you’re fabricating a frame made up of several beams joined together at different points. If you opt for backstep skip welding, you would start at one end and work your way towards the opposite side while constantly backtracking along each joint as you progress forward.
In contrast, if you choose intermittent skip welding, you might divide the joints into shorter intervals and leave small gaps between each section when welding.
These visual references should give you a clearer idea of how backstep and intermittent skip weld patterns differ from one another.
AWS Standards for Skip Weld Symbols:
When it comes to representing skip welded joints, the American Welding Society (AWS) A2.4 provides essential guidelines and standards. These standards ensure that skip weld symbols are accurately represented on engineering drawings for seamless communication between fabricators and welders.
The AWS has specific requirements and recommendations regarding the representation of skip welds. According to their standards, a backstep skip weld consists of a weld symbol, weld size, pitch and length of skip weld as shown in example above.
How to Show a Skip Weld? – Step-by-step guide on how to accurately depict a skipped joint using appropriate techniques
When it comes to showing skip welds on drawings, precision and clarity are of utmost importance. By following the correct procedures, you can ensure that the symbol accurately represents the intended skipped joints.
Here is a step-by-step guide on how to effectively show a skip weld:
⚡️ 1. Begin by identifying and understanding the location and type of skip weld required based on the project specifications or welding procedure instructions.
⚡️ 2. Select an appropriate arrow line for indicating the position of each skipped joint. The length and spacing between these arrows should be consistent with their intended placement.
⚡️ 3. Draw one full reference line across all areas where welding will occur, including both continuous welds and skipped joints.
⚡️ 4. Place small dots or short perpendicular lines along this reference line at positions corresponding to the centerline of each omitted joint.
⚡️ 5. Connect each dot or perpendicular line with two parallel dash lines extending towards adjacent full reference lines, forming an X shape known as ‘skip marks.’
⚡️ 6. Above each skip mark, draw an arrow representing the direction in which welding will recommence after skipping that particular joint.
⚡️ 7. Add necessary dimensions, if required, indicating spacing or intervals between successive skips for intermittent skip welds.
⚡️ 8.Ensure proper labeling by including any relevant information such as size specifiers or other notes alongside the symbol representation of skip welds.
By following these steps carefully, you can create clear and concise representations of skip weld symbols that accurately convey your intentions during fabrication processes
Comparing Skip Welds vs Stitch Welds
Skip welds and stitch welds are both commonly used welding techniques in various industries where strong, reliable joints are required. While they share similarities in terms of their intermittent nature, there are distinct differences between these two methods.
🛑 One primary difference lies in their application. Skip welds are typically used to reduce heat input, minimize distortion, or conserve time and materials. They provide sufficient strength while requiring fewer passes than continuous welds. On the other hand, stitch welds are often utilized for joining thin sheets or making short intermittent runs along a joint.
🛑 Another contrast is seen in their appearance and structural integrity. Skip weld symbols indicate that the intermittent beads need to fully penetrate the workpiece at each location specified on the drawing. This creates a stronger joint compared to stitch welding which only requires small tack-like spots between gaps.
🛑 Each technique carries its own set of advantages and disadvantages as well. Skip welding decreases overall heat input into the material, reducing potential distortion or warping during fabrication. Additionally, it can be a time-saving method as it eliminates lengthy continuous bead runs along non-critical areas of a joint without compromising strength requirements.
🛑 In contrast, stitch welding allows for effective control over heat input due to frequent starts and stops but may require more passes to achieve desired penetration depth throughout the entire joint length.
Conclusion:
In conclusion, skip weld symbols are an essential aspect of welding that must be understood and applied correctly for successful fabrication. By recapping the key points discussed in this article, we can reinforce the importance of understanding skip weld symbols in welding practices.
Firstly, skip welds can be classified into two types: backstep skip welds and intermittent skip welds. Backstep skip welds involve a systematic progression of skipping specified lengths along the joint, while intermittent skip welds consist of randomly spaced skips along the joint. Both types have their own advantages and applications depending on factors such as joint strength requirements and material thickness.
Secondly, it is crucial to distinguish between stitch welds and skip welds in order to avoid confusion. While both techniques involve interrupted or skipped portions along a joint, they serve different purposes. Stitch welding is primarily used for tacking or temporarily holding pieces together before final full-length welding, whereas skip welding involves intentionally leaving gaps between welded sections to promote better heat dissipation and reduce stress concentrations.
Lastly, adherence to specific guidelines set by organizations such as AWS (American Welding Society) is vital when depicting skip weld symbols on drawings. Following these standards ensures clear communication among fabricators regarding correct welding methods for each section of a project.
Understanding how to interpret and apply Skip Weld Symbols will enable professionals in the field of welding to enhance their craftsmanship while achieving optimal structural integrity. By mastering this skill, they ensure consistency across various projects and contribute towards fulfilling industry standards efficiently.