What is Stitch Welding?
Stitch welding is a welding technique where a series of intermittent welds, or “stitches,” are made along a joint or seam instead of a continuous weld.
These individual welds are spaced apart, leaving gaps between them. Stitch welding is commonly used in various applications for specific purposes.
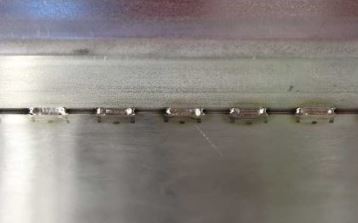
What should be minimum length of stitch welds?
The minimum length of stitch welds can vary depending on the specific welding application, material thickness, and welding code or standard being followed.
However, as a general guideline, stitch welds are typically recommended to have a minimum length of three times the diameter of the electrode being used. This guideline helps ensure sufficient fusion and strength in the weld joint.
It is important to note that specific welding codes or standards such as AWS D1.1 may provide more detailed requirements or recommendations for minimum stitch weld lengths based on the specific application and material being welded. Also, Stitch welding symbol in drawing usually specify the length.
Applications of Stitch Welding
Here are some of its applications:
- Sheet metal fabrication: Stitch welding is often used in sheet metal fabrication to join thin metal sheets together. It helps prevent distortion and warping that can occur with continuous welding on thin materials.
- Automotive industry: Stitch welding is employed in the automotive industry for various purposes, such as joining body panels, reinforcing structural components, or attaching brackets. It provides strength and rigidity while minimizing heat distortion.
- Pipe and tube welding: Stitch welding is used in pipe and tube welding applications, especially when welding thin-walled pipes or tubes. It helps control heat input and reduces the risk of burn-through.
- Repair and maintenance: Stitch welding is useful for repair and maintenance tasks, such as patching or reinforcing damaged areas. It allows for localized repairs without affecting the entire structure.
- Temporary fixturing: Stitch welding can be used as a temporary fixturing method to hold components or parts in place during assembly or fabrication processes. The intermittent welds can be easily removed when no longer needed.
Advantages of Stitch Welding
- Reduced heat input
- Minimized distortion
- Improved control over the welding process
- Suitable for thin materials
- Can be used for localized repairs or reinforcement
- Allows for temporary fixturing
Disadvantages of Stitch Welding
- May require more time and labor compared to continuous welding
- Potential for reduced overall strength compared to continuous welds
- Increased risk of stress concentration at the stitch weld locations
- Limited suitability for high-stress or high-pressure applications
- Requires careful planning and consideration of stitch spacing and size to ensure adequate strength and integrity.