What is a Tack Weld?
Tack welding is a temporary welding technique that involves using low heat and a short welding arc to join metal pieces together temporarily, prior to the welding to complete joint. Its primary function is to secure the metal components in position, preventing any movement or misalignment during the sheet metal welding procedure.
Without tack welding, achieving precise welds according to specifications would be nearly impossible and accuracy would be extremely challenging.
The purpose of tack welding is to hold the workpieces firmly in place, ensuring their proper location, spacing, and alignment until the final welding is performed. In essence, tack welds serve as temporary fixtures during the setup of the workpieces. Additionally, these welds need to possess sufficient strength to withstand significant stresses.
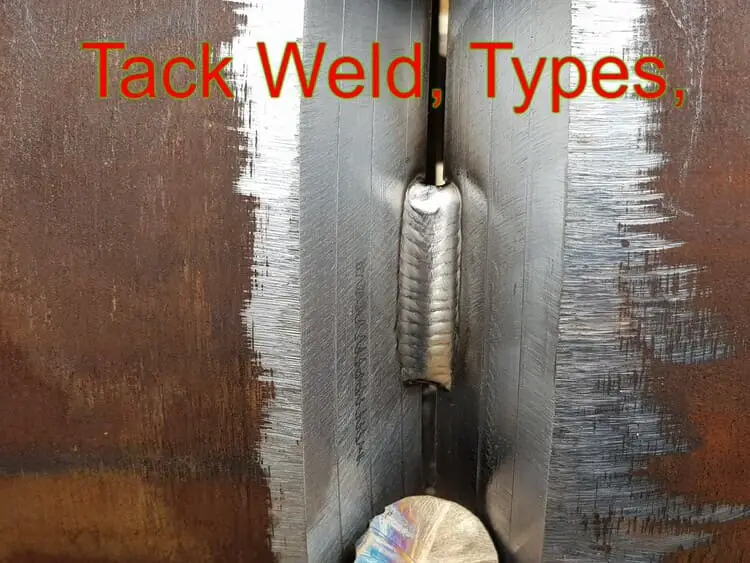
Materials for Tack Welding
Tack welding can be performed on any metal that is suitable for welding. However, the approach used in tack welding sets it apart from other welding techniques. Mainly, same material as the base metal is used for tack welding either deposited by welding or using small metal pieces, known as bullet tack welds.
Furthermore, the ease of tack welding varies depending on factors such as the thickness and type of material. Thin materials with lower melting points present more difficulties in tack welding compared to others.
Tack Weld Symbol
The tack weld symbol is a graphical representation used in welding blueprints and drawings to indicate the location and size of tack welds. It consists of a small triangle or circle placed at the intersection of the reference line and the joint to be tack welded.
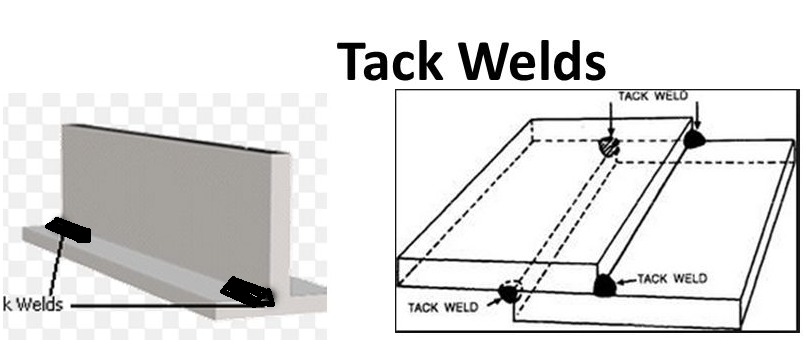
Minimum and maximum size of Tack welds
The minimum and maximum size of tack welds can vary depending on the specific welding code, industry standards, and the application requirements. However, here are some general guidelines:
Minimum Size of Tack Welds
The minimum size of tack welds is typically specified to ensure sufficient strength and fusion. As per AWS D1.1 welding code, it require a minimum tack weld length of 3 times the thickness of the thinner part being joined, or a minimum of 6 mm (0.24 inches), whichever is greater, for fillet weld tack welds.
Maximum Size of Tack Welds
The maximum size of tack welds is generally not explicitly specified in welding codes or standards. Unlike minimum size requirements, the maximum size of tack welds is typically kept to 2-inch or 50 mm, taking into consideration factors such as joint fit-up, distortion control, and welding process efficiency.
While there is no specific numerical limit, it is generally recommended to keep tack welds as small as possible while still ensuring they provide sufficient temporary support and alignment for the workpieces. Large tack welds can consume excessive filler material, create excessive heat input, and potentially lead to distortion or other welding issues.
Types of Tack Welds
There are various types of tack welding, each with its own specific use and purpose. Let’s highlight the five most common types:
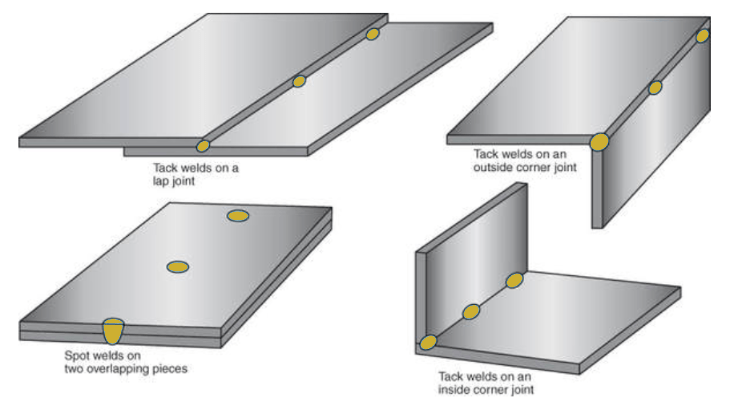
- Standard Tack Weld:
The standard tack weld is suitable when providing support for the final weld is a consideration. This type of weld is typically large enough to bear the weight of the welded materials, preventing them from breaking off. However, it’s important not to make the tack welds too large so that they can be easily consumed by the final weld. - Bridge Tack Weld:
Bridge tack welding is used when there is a gap that needs to be filled between the materials after they have been fitted together. This gap may be a result of errors in cutting the material or distortion in the supplied materials. Bridge tack welding involves applying small tack welds alternately on each component. The alternating tacking allows one side to cool before re-tacking. Flux-Cored welding, Mig, and Tig welding methods work well for this type of tacking as they are easily controllable. - Thermit Tack Weld:
Thermit tack welding involves mixing pure magnesium metal, aluminum powder, and iron oxide powder. The resulting reaction produces extremely high temperatures, often exceeding 4000 degrees Fahrenheit. This method is used for specialized applications that require intense heat for joining specific materials. - Hot Tacking:
Hot tacking involves depositing excess filler metal in the gap area between metal parts. The purpose is to use the weld to bridge the gap between the parts. Hot tacking is employed when contact between the welded component members is important, but other factors prevent direct contact. In this method, similar to bridge tacking, a weld is used to bridge the parts together, and then a sledgehammer is used to strike the parts into place.
It’s worth noting that these are just a few examples of common tack welding techniques, and there may be other specialized methods depending on the specific requirements of the welding project.
Advantages of tack welding
- Improved support for the final weld.
- Helps maintain proper alignment and positioning of the workpieces.
- Facilitates ease of welding by preventing movement or misalignment during the welding process.
- Reduces the risk of distortion or warping of the materials being welded.
- Allows for easier adjustment or repositioning of components before final welding.
- Provides temporary strength and stability to hold the workpieces together.
- Saves time and effort by ensuring accurate and secure placement of the materials prior to final welding.
Disadvantages of tack welding
- Tack welds are temporary and may not provide the same level of strength and durability as the final weld.
- Tack welding requires additional time and effort to perform, as it involves multiple welds to secure the workpieces.
- If tack welds are not properly positioned or sized, they can interfere with the final weld or require additional cleanup.
- Tack welding may create additional heat-affected zones (HAZ) in the workpieces, which can affect the overall structural integrity.
- Tack welds may need to be removed or modified if adjustments or changes are required during the welding process, adding extra work.
- In some cases, tack welding may not be suitable for certain materials or welding processes, limiting its applicability.
- Tack welding can introduce additional stress concentrations or weak points in the weld joint.
- If tack welds are not properly executed, they may result in misalignment or movement of the workpieces, affecting the overall quality of the final weld.
How to weld perfect tack weld?
To achieve a perfect tack weld, follow these steps:
- Clean the workpieces: Ensure that the surfaces to be welded are clean and free from any contaminants such as rust, oil, or dirt. Use a wire brush or appropriate cleaning method to prepare the surfaces.
- Set up the workpieces: Position the workpieces in the desired alignment and secure them using clamps or fixtures. Proper alignment is crucial for achieving accurate tack welds.
- Choose the appropriate welding process: Select the welding process that is suitable for the materials being welded and the specific application. Common processes include shielded metal arc welding (SMAW), gas metal arc welding (GMAW/MIG), or gas tungsten arc welding (GTAW/TIG).
- Prepare the welding equipment: Set up the welding machine according to the recommended settings for the chosen process and the thickness of the materials. Ensure that the welding machine is in good working condition.
- Position the electrode or welding gun: Hold the electrode or welding gun at the correct angle and distance from the workpiece. The angle and distance will depend on the welding process and the joint configuration.
- Execute the tack weld: Depress the welding trigger or strike an arc to initiate the welding process. Keep a steady hand and move the electrode or welding gun along the joint to create a tack weld. The tack weld should be of sufficient size and penetration to hold the workpieces securely.
- Control heat input: Be mindful of the heat input to avoid excessive distortion or damage to the workpieces. Use short welding arcs and adjust the welding parameters as needed to achieve the desired results.
- Inspect the tack weld: After completing the tack weld, visually inspect the joint to ensure proper fusion, absence of defects, and satisfactory penetration. Make any necessary adjustments or repairs if the tack weld is not up to standard.
- Repeat as necessary: Depending on the project and joint configuration, repeat the tack welding process at appropriate intervals along the joint to secure the workpieces adequately.
Why tack weld cracks?
Tack welds can potentially crack due to several factors, including:
- Insufficient Fusion: If the tack weld does not achieve proper fusion between the base metal and the filler metal, it can create a weak point that is susceptible to cracking. Insufficient heat input, incorrect welding parameters, or poor technique can lead to incomplete fusion and weakened tack welds.
- High Residual Stress: During the welding process, localized heating and subsequent cooling can induce residual stresses in the weld and surrounding areas. Tack welds, being smaller and concentrated, can experience higher stress concentrations, which may contribute to crack initiation and propagation.
- Inadequate Preheating: In some cases, preheating of the workpieces before tack welding may be necessary, especially for thicker or highly restrained joints. Insufficient preheating can result in thermal stress buildup and potential cracking.
- Improper Joint Preparation: If the joint preparation is inadequate or improper, it can lead to poor fit-up or gaps between the workpieces. These gaps can cause stress concentration and promote crack formation during tack welding.
- Material Incompatibility: Incompatible materials or dissimilar metals can create unfavorable metallurgical conditions, such as increased susceptibility to cracking due to different thermal expansion rates or chemical reactions between the materials.
- Rapid Cooling: Tack welds, being small in size, cool down relatively quickly compared to larger welds. Rapid cooling can increase the risk of cracking, especially in materials with high hardenability or high carbon content.
- Poor Welding Technique: Inadequate welding technique, such as excessive heat input, erratic arc starts/stops, or improper travel speed, can result in undesired weld characteristics and potential cracking.
To minimize the risk of tack weld cracking, it is important to follow proper welding procedures, use appropriate welding parameters, ensure proper joint fit-up, select compatible materials, and control heat input and cooling rates. Additionally, conducting visual inspections and non-destructive testing methods can help identify and address potential cracking issues.