Linear Indication in Welding
Linear indication is a term used in welding to describe a test result where a defect or discontinuity in the material appears as a linear or aligned array.
These indications can be caused by various factors such as porosity, incomplete penetration, slag inclusion, lack of fusion, and more. Identifying and addressing linear indications is crucial to ensure the overall quality and integrity of welded joints.
“Linear Indications: Indications that have a length greater than three times their width are referred to as elongated indications. “
Types of Indication in Welding
In welding, there are three main types of indications that can occur, each providing insights into the presence of defects or discontinuities in the weld joint:
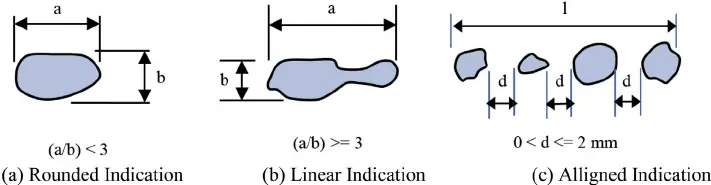
Linear Indication
A linear indication appears as a continuous line or aligned array. It can be caused by factors such as incomplete penetration, lack of fusion, slag inclusion, or thermal/mechanical stresses. Detection methods include visual inspection, radiographic testing, or ultrasonic testing.
Elongated Indication
An elongated indication is a type of linear indication that appears stretched or lengthened compared to its width.
Similar to linear indications, elongated indications can be caused by factors such as incomplete penetration, porosity, lack of fusion, slag inclusion, and others.
Rounded Indication
Indications that have a length equal to or smaller than three times their width are categorized as rounded indications. These rounded indications can take various shapes, including circular, elliptical, conical, or irregular, and may even have tails.
When evaluating the size of a rounded indication, the tail should be considered as well. Rounded indications can be seen on radiographs and may result from any imperfection in the weld, such as porosity, slag, or the presence of tungsten.

A rounded indication is a defect that appears as a circular or spherical shape. It can be caused by factors such as gas bubbles trapped in the weld metal, shrinkage cavities, or irregularities in the weld profile. Rounded indications are often detected through visual inspection or non-destructive testing methods.
Acceptance Criteria for Linear Indications as per ASME BPVC Section VIII Div 1
- Cracks, Lack of Penetration, and Lack of Fusion:
Any form of cracking, lack of penetration, or lack of fusion will not be accepted in the weld joint. - Elongated Indications:
Any elongated indication that exceeds specific lengths depending on the thickness of the weld metal shall be considered unacceptable. The criteria are as follows:- For T up to 19 mm (3/4 in.), the length should be greater than 6 mm (1/4 in.).For T greater than or equal to 19 mm (3/4 in.) and less than or equal to 57 mm (2-1/4 in.), the length should be greater than T/3, where 19 mm ≤ T ≤ 57 mm.For T greater than 57 mm (2-1/4 in.), the length should be greater than 19 mm (3/4 in.).
Acceptance Criteria for Rounded Indications (Mandatory Appendix 4)
According to Mandatory Appendix 4, rounded indications exceeding certain dimensions should be considered relevant. The acceptance criteria are as follows:
- For T less than 3 mm (1/8 in.), the rounded indication should exceed T/10.
- For T ranging from 3 mm to 6 mm (1/8 in. to 1/4 in.), inclusive, the rounded indication should exceed 0.5 mm (1/64 in.).
- For T greater than 6 mm (1/4 in.) to 50 mm (2 in.), inclusive, the rounded indication should exceed 1.0 mm (1/32 in.).
- For T greater than 50 mm (2 in.), the rounded indication should exceed 1.5 mm (1/16 in.).
Additionally, Mandatory Appendix 4 provides tables, charts, and figures as references for acceptance or rejection criteria related to rounded indications in welding.
Factors Causing Linear Indications
Linear indications can be attributed to several factors commonly found in welding applications. These include:
- Porosity: The presence of gas pockets or voids in the weld metal can manifest as linear indications. Usually, porosity are rounded indications.
- Incomplete Penetration: Insufficient penetration into the base material can result in linear indications along the weld.
- Slag Inclusion: Entrapment of slag within the weld can create linear indications.
- Lack of Fusion: Inadequate fusion between the weld metal and base material can lead to linear indications.
- Thermal or Mechanical Stresses: Linear indications may also arise from stresses induced during welding processes.
Detecting Linear Indications
Identifying linear indications can be challenging, requiring specialized testing methods and careful inspection. Some key points to consider are:
- Specialized Testing: Employing techniques like radiographic testing or ultrasonic testing can help reveal hidden linear indications.
- Visual Inspection: Careful visual examination, including the use of magnifying devices, can aid in detecting subtle linear indications.
- Hidden Indication: Linear indications may be concealed by other weld defects, such as underbead cracks or slag inclusions. Thorough inspection is necessary to uncover them.
Elongated Indication in Radiography
An elongated indication refers to a linear indication that appears stretched or lengthened compared to its width. Similar to regular linear indications, elongated indications can be caused by factors like incomplete penetration, porosity, slag inclusion, lack of fusion, and others.
Identification of Weld Defects
Weld defects can be identified through various inspection methods, including:
- Visual Inspection: Examining the weld surface for visible signs of defects like cracks, porosity, or inadequate fusion.
- Ultrasonic Testing: Using high-frequency sound waves to detect internal defects or inconsistencies in the weld.
- Radiographic Testing: Employing X-ray or gamma-ray imaging to reveal hidden defects within the weld.
- Magnetic Particle Testing: Applying magnetic particles to detect surface-breaking defects like cracks.
- Penetrant Testing: Applying a liquid dye to identify surface-breaking defects that may not be visible to the naked eye.