The “grind flush” weld symbol is used in welding drawings to indicate that the weld surface needs to be ground flush or leveled after welding.
The welder would perform the welding operation as indicated by other welding symbols on the drawing, and after the welding is complete, they would use a grinding tool or process to remove any excess weld material until the surface is flush and smooth, matching the surrounding base metal.
What is meant by Flush Grind Weld?
A flush grind weld refers to a specific type of weld joint where the weld bead is ground or smoothed down to create a flush or seamless surface with the base metal.
In this welding technique, the weld bead is intentionally blended or ground down using abrasive tools or grinding equipment until it is level with the surrounding surface.
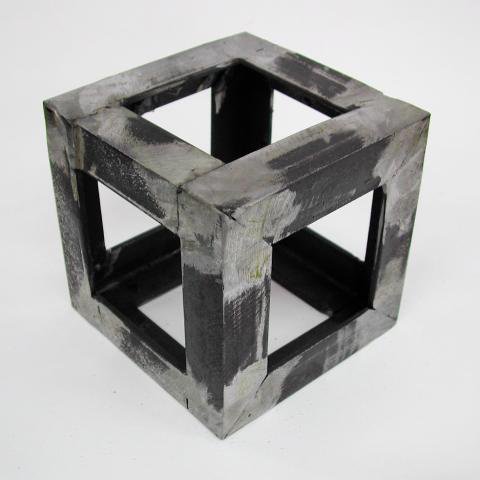
The purpose of performing a flush grind weld is to eliminate any visible or protruding weld bead, creating a smooth and aesthetically pleasing finish.
This welding technique is commonly used in applications where the appearance of the welded joint is important, such as in architectural structures, automotive bodywork, or decorative metalwork.
In addition to improving the visual appeal, a flush grind weld can also provide functional benefits. By removing any sharp edges or irregularities caused by the weld bead, it helps to minimize the risk of stress concentration points, corrosion, or potential damage to surrounding components.
Grind Flush Weld Symbol
In welding, a grind flush weld symbol is a graphical representation used on technical drawings or welding blueprints to indicate that a weld bead should be ground or smoothed down until it is flush with the surrounding surface.
The grind flush weld symbol consists of a straight line segment called a reference line, along with additional symbols or annotations placed on or near the reference line.
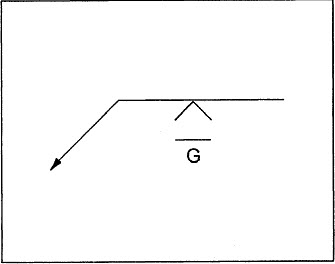
The symbol may vary slightly depending on the specific standard or code being followed, but it generally includes the following elements:
- Reference Line: A horizontal line that represents the path of the weld joint.
- Arrow: An arrowhead is typically added at one or both ends of the reference line to indicate the extent or direction of the weld joint.
- Tail: A short vertical line or tail is attached to the reference line at one or both ends. This tail may contain additional symbols or annotations.
- Grind Flush Symbol: The grind flush symbol is a small horizontal line placed above the weld symbol with a letter “G“. It represents the requirement to grind or smooth the weld bead until it is flush with the base metal.
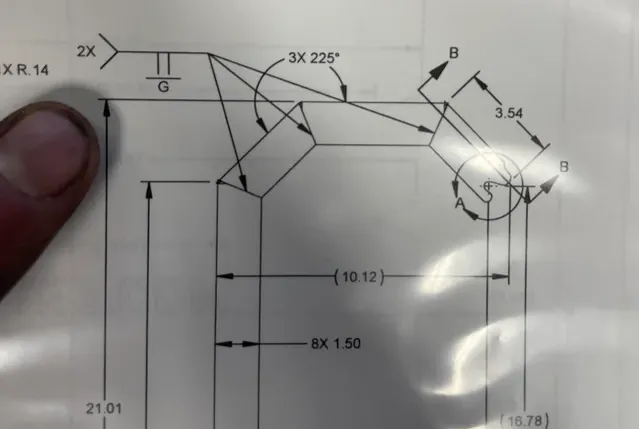
Grind Flush Weld Symbol for Fillet Weld
The grind flush weld symbol for a fillet weld, indicating that the weld bead should be ground or smoothed down until it is flush with the surrounding surface, can be represented using the following graphical symbol:
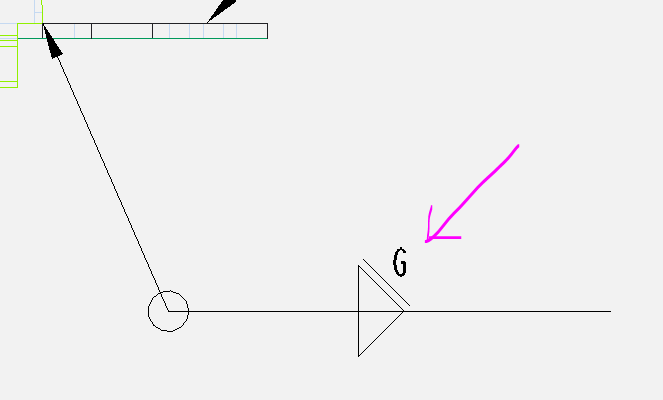
In most standards or codes, the grind flush symbol for a fillet weld consists of a fillet weld symbol with additional supplementary contour symbol.
Advantages of Grind Flush Weld
Grind flush welds offer several advantages, both from a functional and aesthetic standpoint. Here are some of the key advantages of using grind flush welds:
- Improved Appearance: Grinding down the weld bead until it is flush with the surrounding surface results in a seamless and smooth appearance. This eliminates visible weld beads or protrusions, creating a clean and aesthetically pleasing finish. Grind flush welds are commonly used in applications where the visual appeal is crucial, such as architectural structures, automotive bodywork, or decorative metalwork.
- Reduced Stress Concentration: By grinding down the weld bead, any sharp edges or irregularities are removed, reducing stress concentration points in the welded joint. This helps distribute the load more evenly across the joint, minimizing the potential for stress-induced failures or crack initiation.
- Corrosion Resistance: Weld beads can sometimes act as potential sites for corrosion initiation, particularly if they are exposed to corrosive environments. Grind flush welds eliminate the crevices or recesses created by weld beads, reducing the likelihood of corrosion and enhancing the overall corrosion resistance of the joint.
- Enhanced Cleanability: Weld beads can be challenging to clean, especially in applications where cleanliness is essential, such as food processing equipment or sanitary environments. Grind flush welds facilitate easier cleaning since there are no protruding or uneven surfaces that can trap debris or contaminants.
- Compatibility with Coatings: For applications requiring surface coatings or finishes, grind flush welds provide a smoother surface that is more conducive to proper adhesion and uniform application of coatings. Coatings can be applied more effectively and consistently on a flush, even surface, ensuring optimal protection and performance.
- Improved Safety: The removal of sharp edges or protrusions through grind flush welds helps enhance safety by reducing the risk of accidental cuts, scrapes, or snagging on the welded joint. This is particularly important in applications where personnel may come into contact with the welded surfaces.
Best welding process for Flush Grind Welds
The choice of the best welding process for flush grind welds depends on various factors such as the type of material, joint design, thickness, and specific application requirements.
However, certain welding processes are commonly used for achieving flush grind welds. Here are a few welding processes that are often suitable for flush grind welds:
Gas Metal Arc Welding (GMAW/MIG)
Gas Metal Arc Welding, commonly known as MIG (Metal Inert Gas) welding, is a widely used process for achieving flush grind welds. It involves the use of a continuous wire electrode that is fed through a welding gun.
The weld bead can be easily controlled and manipulated, allowing for precise control over the size and shape of the weld. MIG welding offers good control over the weld pool, making it suitable for achieving flush and smooth welds that require minimal post-weld grinding.
Gas Tungsten Arc Welding (GTAW/TIG)
Gas Tungsten Arc Welding, also known as TIG (Tungsten Inert Gas) welding, is another commonly used process for flush grind welds. TIG welding utilizes a non-consumable tungsten electrode to create an arc and a separate filler material, if needed.
The process allows for precise control over the heat input and weld pool, producing clean and precise welds. TIG welding is well-suited for achieving flush and smooth welds in thin materials and applications where high-quality aesthetics are crucial.
Shielded Metal Arc Welding (SMAW)
Shielded Metal Arc Welding, commonly known as stick welding, is a versatile welding process suitable for achieving flush grind welds. It involves the use of a consumable electrode coated with a flux that creates a protective shield during the welding process.
Stick welding is often used for structural applications and can deliver strong and durable welds. While it may require more post-weld grinding compared to other processes, it can still achieve flush and smooth welds when executed with care.
Flux-Cored Arc Welding (FCAW)
Flux-Cored Arc Welding is a process similar to MIG welding but uses a tubular wire electrode filled with flux. FCAW can be performed with or without shielding gas, depending on the specific application.
It offers high deposition rates and good penetration, making it suitable for achieving flush grind welds in thicker materials and structural applications.