What is Backing Gas in Welding?
Backing gas in welding refers to the inert gas or gas mixture used to protect the backside of a weld joint from atmospheric contamination during the welding process.
It is commonly employed in processes such as TIG (Tungsten Inert Gas) welding and some forms of MIG (Metal Inert Gas) welding.
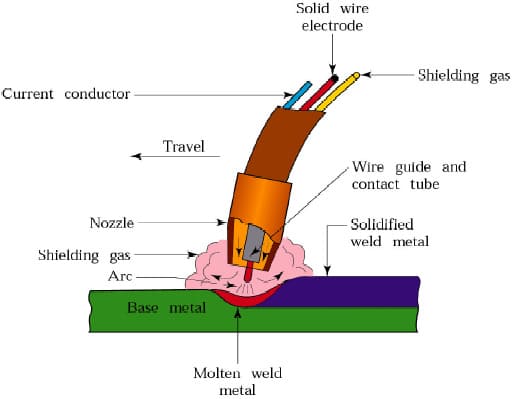
The primary purpose of using backing gas is to prevent oxidation and other detrimental reactions that can occur when the molten weld pool comes into contact with air.
By introducing an inert gas, such as argon or helium, on the backside of the weld joint, a shield is created that displaces the surrounding atmosphere.
This shield effectively isolates the weld area from oxygen, nitrogen, and other reactive gases, minimizing the risk of defects and ensuring the integrity of the weld.
Types of Backing Gases
There are several types of gases commonly used as backing gases in welding processes. The choice of backing gas depends on factors such as the weld material, welding process, and desired weld characteristics. Here are some of the commonly used backing gases:
- Argon: Argon is one of the most widely used backing gases in welding. It is an inert gas that effectively displaces the surrounding atmosphere and provides excellent shielding properties. Argon is commonly used for stainless steel, aluminum, and other non-ferrous metals welding applications.
- Helium: Helium is another inert gas used as a backing gas in welding. It offers higher heat conductivity compared to argon, making it suitable for applications that require higher heat input. Helium is often used for welding thicker materials and can help improve penetration.
- Argon-Helium Mixtures: Gas mixtures combining argon and helium are commonly used as backing gases. These mixtures provide a balance between the benefits of both gases. The addition of helium to argon can enhance heat transfer, increase arc stability, and improve penetration. The specific ratio of argon to helium in the mixture can be adjusted based on the welding requirements.
- Nitrogen: While not as commonly used as argon or helium, nitrogen can be used as a backing gas in certain welding applications. It is less expensive compared to argon and helium but may have different effects on the weld characteristics. Nitrogen is often used for welding certain ferrous metals, such as carbon steel.
- Carbon Dioxide (CO2): In some cases, carbon dioxide can be used as a backing gas, particularly in certain welding processes like submerged arc welding (SAW). CO2 can provide some level of shielding and prevent oxidation during welding.
Difference between Trailing, Backing and Shielding gas during welding process
During the welding process, different gases are used for various purposes, including trailing gas, backing gas, and shielding gas.
Here’s a breakdown of the differences between these gases:
Trailing Gas
Trailing gas, also known as post-flow gas, refers to the gas flow that continues after the welding arc is extinguished. It serves the purpose of shielding the hot weld bead and electrode from oxidation as they cool down.
The trailing gas helps to prevent the formation of defects and ensures the integrity of the weld as it solidifies.
Generally, the trailing gas is the same as the shielding gas used during the welding process, maintaining a continuous and protective atmosphere until the weld cools sufficiently.
Backing Gas
Backing gas is used to protect the backside of a weld joint during the welding process. It creates a shield between the molten weld pool and the surrounding atmosphere, preventing oxidation and other detrimental reactions.
The primary role of backing gas is to ensure the integrity and quality of the weld by minimizing the risk of defects. Inert gases like argon or helium are commonly used as backing gases due to their inert properties.
The choice of backing gas depends on the welding process and materials being welded.
Shielding Gas
Shielding gas is employed to protect the weld zone from atmospheric contamination during the welding process.
It creates a protective envelope around the arc and the molten weld pool, preventing reactions with oxygen, nitrogen, and other reactive gases that could compromise the quality of the weld.
The shielding gas is typically an inert gas or a gas mixture, such as argon, helium, or a combination of both. The selection of a suitable shielding gas depends on factors such as the welding process, base materials, and desired weld characteristics.
Shielding gas is essential in processes like TIG (Tungsten Inert Gas) welding and some forms of MIG (Metal Inert Gas) welding.
What is purge gas in welding?
Purge gas in welding refers to the gas or gas mixture used to create and maintain a protective atmosphere within a confined space during welding. It is commonly used in applications where welding is performed on the internal surfaces of pipes, tubes, or other closed structures.
The primary purpose of using purge gas is to prevent the oxidation and contamination of the internal weld area. When welding in a confined space, such as inside a pipe, the absence of proper gas shielding can lead to the formation of defects, such as porosity, lack of fusion, or excessive oxidation. Purge gas helps to mitigate these issues by displacing the surrounding air and creating a controlled and oxygen-free environment for the weld.
Typically, an inert gas, such as argon or helium, is used as a purge gas. These gases have low reactivity and do not react with the hot metal or other components of the weld. The choice of purge gas depends on factors such as the material being welded, the welding process, and the desired weld quality.
During the welding process, the purge gas is introduced into the internal space through one or more access points, while any excess gas and contaminants are allowed to exit through another opening. This continuous flow of purge gas ensures the removal of oxygen and other reactive gases from the weld area, creating a clean and shielded environment.
Proper control of the purge gas flow rate, pressure, and distribution is crucial to maintain an effective shielding atmosphere. Welding standards and guidelines may provide specific recommendations for purge gas parameters based on the welding application and the desired quality of the weld.
What is trailing gas in GTAW?
In GTAW (Gas Tungsten Arc Welding), trailing gas refers to the flow of shielding gas that continues after the welding arc has been extinguished. Also known as post-flow gas, its purpose is to shield the weld zone and electrode as they cool down after welding.
During GTAW, an inert gas, typically argon, is used as the shielding gas. This gas flows through the welding torch to create a protective atmosphere around the arc and the molten weld pool, preventing atmospheric contamination and ensuring the quality of the weld.
Once the welding arc is turned off, trailing gas continues to flow for a specified duration. The duration of the trailing gas flow is typically set based on factors such as the material being welded, the welding parameters, and the desired cooling rate of the weld.
The trailing gas serves several important functions:
- Shielding: Trailing gas maintains a protective shield around the hot weld bead and electrode as they cool down. This shield prevents oxidation and other reactions with the surrounding air, which could lead to defects in the weld.
- Cooling: Trailing gas helps to cool the weld zone and reduce the risk of overheating. It promotes controlled solidification of the weld, which can enhance the mechanical properties and reduce the likelihood of cracking.
- Gas Coverage: The continuous flow of trailing gas helps to displace any residual gases or fumes from the weld area, ensuring a clean and uncontaminated surface.
The duration of trailing gas flow varies depending on the specific welding application. It is typically set by the welder or specified in welding procedures, taking into account factors such as the material thickness, joint configuration, and welding conditions.