What is Arc Length in Welding?
In welding, arc length refers to the distance between the tip of the welding electrode or welding wire and the surface of the workpiece being welded. It is the gap through which the electric arc is maintained during the welding process.
The arc length plays a crucial role in determining the quality and characteristics of the weld. It affects factors such as heat input, penetration, and weld bead shape. The ideal arc length varies depending on the welding process, material being welded, and the specific welding parameters.
Why is arc length important in welding?
Maintaining a proper arc length is important for achieving a stable arc and controlling the heat input. If the arc length is too long, the arc may become unstable, leading to spatter, poor penetration, and an irregular bead shape.
On the other hand, if the arc length is too short, it can cause excessive heat input, resulting in burn-through, distortion, and a wider, flatter bead.
Welders need to maintain a consistent and appropriate arc length by adjusting the welding technique, such as the angle and travel speed, to achieve the desired weld quality.
Welding Arc Length Basics
In welding, the arc length is responsible for controlling the width and quality of the weld. If the arc length is too short, the resulting weld bead will be tall, narrow, and cold, potentially leading to fusion defects.
On the other hand, if the arc length is too long, it can cause increased spatter and undercut defects at the weld toes. The resulting weld will be wide and flat, but may suffer from reduced penetration as the arc energy is spread out rather than concentrated.
To understand this concept better, envision the welding arc as having a “point-to-plane” geometry, with the electrode as the point and the workpiece as the plane. As the distance between the electrode and workpiece increases, the arc widens at its base, resulting in a wider weld bead.
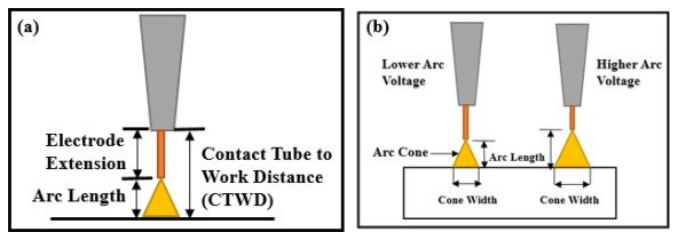
As depicted in the right-hand portion (b), the arc formed between the electrode and workpiece resembles a cone shape in a point-to-plane configuration. When the distance between the electrode and workpiece is increased, the base of the cone widens. This widening corresponds to the circular region where the arc makes contact with the workpiece.
Arc length also affects arc voltage, especially in processes like stick welding (SMAW) or TIG welding (GTAW), where the voltage is controlled by the arc length. As the arc length increases, the voltage also increases, and vice versa.
For instance, in stick welding, the open circuit voltage is around 80 volts, but when the arc is established, it drops to about 20 volts. Shortening the arc length reduces the voltage, resulting in a colder and narrower weld.
If the arc length becomes too short, the arc may extinguish. Conversely, lengthening the arc increases the voltage, leading to a wider and flatter weld bead, accompanied by a more erratic and spattery arc. If the arc length exceeds a certain point, the voltage becomes too high to maintain the arc, causing it to extinguish.
In processes like MIG welding, where the voltage is set by the welding machine, the arc length is indirectly controlled by adjusting the wire feed rate. If the wire feed rate increases, the arc length tends to shorten, causing the voltage to drop.
However, the power source compensates by increasing the amperage to maintain the set voltage. This ensures a consistent arc length. In MIG and similar processes, the current level is determined by the wire feed rate.
The total electrical energy in a welding arc is influenced by both the amperage (current) and voltage. Increasing either one results in a hotter arc. Voltage primarily affects the energy that spreads the deposited metal, widens the weld, and improves its bite at the edges. Amperage primarily affects the energy that melts the filler metal and penetrates into the base metal beneath the surface.
What is the correct arc length?
The correct arc length in welding depends on several factors, including the welding process, electrode type, material thickness, and specific welding requirements. However, as a general guideline, the recommended arc length is typically around 1/8 inch to 3/16 inch (3-5 mm) for most welding processes.
What should the arc length be for stick welding?
The ideal arc length for stick welding, also known as Shielded Metal Arc Welding (SMAW), typically falls within the range of 1/8 inch to 3/16 inch (3-5 mm). This distance refers to the gap between the end of the electrode and the workpiece surface.
How do you control arc length?
Controlling the arc length in welding involves several techniques and considerations. Here are some methods to help maintain and control the desired arc length:
- Electrode angle: Adjusting the angle of the electrode can influence the arc length. Tilting the electrode towards the direction of travel can shorten the arc length, while angling it away can increase the arc length. Experimenting with different angles can help find the optimal position for controlling the arc length.
- Travel speed: The speed at which the welding torch or electrode moves along the joint can affect the arc length. Slowing down the travel speed can shorten the arc length, while increasing the speed can lengthen it. Finding the right balance between travel speed and arc length is crucial for achieving the desired weld quality.
- Stick-out length: Stick-out refers to the length of the electrode extending beyond the contact tip or holder. Adjusting the stick-out length can directly impact the arc length. Increasing the stick-out length can lengthen the arc, while reducing it can shorten the arc. It’s important to follow the manufacturer’s recommendations for the specific electrode being used.
- Welding parameters: Modifying the welding parameters, such as voltage and amperage, can indirectly influence the arc length. Higher voltage and amperage settings tend to create a longer arc, while lower settings result in a shorter arc. It’s essential to follow the recommended parameters for the specific welding process and electrode type.
- Practice and experience: Developing a sense of arc length control comes with practice and experience. Over time, welders become familiar with the sound, appearance, and behavior of the arc, allowing them to make adjustments to maintain the desired arc length.
Types of welding arc length
There are two types of arc length in welding:
- short arc length and
- long arc length.
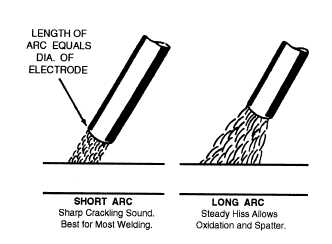
When the arc length is too long, the electrode melts off in large globules, and the arc may frequently break. This results in a wide, spattered, and irregular weld deposit with inadequate fusion between the base metal and the weld.
On the other hand, when the arc length is too short, it fails to generate sufficient heat to properly melt the base metal. This leads to frequent sticking of the electrode to the base metal and produces uneven deposits with irregular ripples.
The recommended arc length is typically equal to the diameter of the bare end of the electrode. However, the specific arc length depends on the type of electrode and the welding process being used.
For smaller diameter electrodes, a shorter arc length is necessary compared to larger electrodes. It’s important to remember that the arc length should generally be about equal to the diameter of the bare electrode, except when welding in the vertical or overhead positions.
In these positions, a shorter arc length is preferred as it provides better control of the molten puddle and helps prevent atmospheric impurities from entering the weld.
What is the importance of a long arc length in stick welding?
Arc length is a critical factor in welding, as it provides valuable information about various aspects of the welding process. It can indicate whether the current is sufficient, whether the welding machine is functioning properly, and whether the environment is cold or hot. Additionally, the arc length can affect the workpiece, particularly if it is cold.
When the intention is to have a long arc with the correct polarity, it helps in keeping the electrode cooler while heating the welded material more effectively. This is especially important when dealing with thick or cold workpieces, starting points, corners, joints, or situations where porosity needs to be avoided, and adequate penetration is required.
In such cases, the rise of slag inside the weld pool is necessary. The temperature of the weld pool is crucial because it is highly intense and can vary significantly, influencing diffusion, convection, concentration, density, and surface tension.
Furthermore, the ability to observe the weld pool is essential. It allows welders to determine if the material is responding in a recognizable manner, indicating similarity to previous work.