What is Welding Preheat?
Welding preheat, also known as preheating, is a process in welding that involves heating the base material to a specific temperature before initiating the welding operation.
The purpose of preheating is to raise the temperature of the base metal in the vicinity of the weld joint to reduce the risk of cracking and improve the quality of the weld.
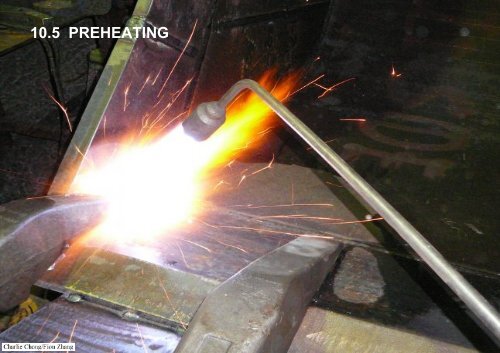
Welding preheat refers to the practice of heating the base metal to a specific temperature before initiating the welding process. This preheating step is performed to minimize the risk of cracking, improve weld penetration, reduce residual stresses, and enhance the overall weld quality.
By carefully controlling the preheat temperature, welders can prevent the formation of brittle microstructures and ensure proper fusion between the base metal and the filler material.
Factors to Consider when Selecting Welding Preheat Temperature
- Material Type: Different materials have different preheat temperature requirements based on their chemical composition and metallurgical properties.
- Thickness: Thicker materials generally require higher preheat temperatures to ensure proper fusion and minimize the risk of cracking.
- Welding Process: The welding process being used, such as MIG/MAG, TIG, or SMAW, can influence the preheat temperature selection.
- Welding Code/Standard: Referencing applicable welding codes and standards provides guidelines and specifications for preheat temperature selection based on specific material and welding requirements.
Preheat temperature table for different materials in Welding
Steel Group | Steel Designation | Carbon Content | Preheat °F.(°C) | ||
Carbon steels | AISI – SAE | 1015 | .13-.18 | 150° | (66°) |
1020 | .18-.23 | 150° | (66°) | ||
1030 | .28-.34 | 200° | (93°) | ||
1040 | .37-.44 | 300° | (149°) | ||
1080 | .75-.88 | 600° | (316°) | ||
Manganese steels | AISI – SAE | 1330 | .28-.33 | 250° | (121°) |
1335 | .33-.38 | 300° | (149°) | ||
1340 | .38-.43 | 350° | (177°) | ||
1345 | .43-.48 | 400° | (204°) | ||
1345H | .42-.49 | 400° | (204°) | ||
Molybdenum Steels | AISI – SAE | 4027H | .24-.30 | 250° | (121°) |
4032H | .29-.35 | 300° | (149°) | ||
4037H | .34-.41 | 350° | (177°) | ||
4042H | .39-.46 | 400° | (204°) | ||
4047H | .44-.51 | 450° | (232°) | ||
Chrome Molybdenum Steels | AISI – SAE | 4118 | .17-.23 | 250° | (121°) |
4130 | .27-.34 | 300° | (149°) | ||
4135 | .32-.39 | 400° | (204°) | ||
4145 | .41-.49 | 500° | (260°) | ||
4145H | .42-.49 | 500° | (260°) | ||
Ni – Chrome MolybdenumandNi – Moly Steel | AISI – SAE | 4340 | .38-.43 | 500° | (260°) |
4615 | .18-.18 | 250° | (121°) | ||
4620 | .17-.22 | 250° | (121°) | ||
4720H | .17-.23 | 300° | (149°) | ||
4820H | .17-.23 | 300° | (149°) | ||
Chromium steels | AISI – SAE | 5015 | .12-.17 | 200° | (93°) |
5046 | .43-.48 | 450° | (232°) | ||
5115 | .13-.18 | 200° | (93°) | ||
5145 | .43-.48 | 450° | (232°) | ||
5160 | .56-.64 | 550° | (288°) | ||
Austenitic ManganeseandChrome – Ni Steels | ASTM | 11-14% Mn | .5-1.3 | Preheat only to remove chill from base metal | |
302 | .15 Max. | ||||
309 | .20 Max. | ||||
310 | .25 Max. | ||||
347 | .08 Max. | ||||
Carbon Steel PlateStructural Quality | ASTM | A36 | .27 Max. | 250° | (121°) |
A131 Gr.B | .21 Max. | 200° | (93°) | ||
A284 Gr.C | .29 Max. | 250° | (121°) | ||
A678 Gr.B (c) | .20 Max. | 200° | (93°) | ||
High Strength Low alloy Steels Structural Quality | ASTM | A131-H.S. | .18 Max. | 350° | (177°) |
A242 Type 2 | .20 Max. | 200° | (93°) | ||
A441 | .22 Max. | 200° | (93°) | ||
A588 Gr.B | .20 Max. | 300° | (149°) | ||
A633 Gr.E | .22 Max. | 250° | (121°) | ||
Alloy and Pressure VesselQuality Steels | ASTM | A514 Gr.F (c) | .10-.21 | 350° | (177°) |
A514 Gr.H (c) | .12-.21 | 300° | (149°) | ||
A514 Gr.Q (c) | .14-.21 | 550° | (288°) | ||
A515 Gr.70 | .35 Max. | 300° | (149°) | ||
A516 Gr.70 | .30 Max. | 250° | (121°) |
Importance of Welding Preheat
- Cracking Prevention: Preheating helps to reduce the cooling rate of the weld, minimizing the potential for cracking. By slowing down the cooling process, preheating allows for the dissipation of hydrogen, which is one of the leading causes of weld cracking.
- Improved Weld Penetration: Preheating raises the base metal temperature, allowing for better weld penetration. This results in stronger and more reliable joints, particularly when working with thick materials or welding dissimilar metals.
- Stress Reduction: Welding generates significant thermal stresses that can lead to distortion and even failure of the welded joint. Preheating helps to minimize these stresses by providing a more uniform temperature distribution throughout the material, reducing the risk of deformation and improving the overall structural integrity.
- Microstructure Control: Certain materials, such as high carbon steels, can form undesirable microstructures during welding, leading to reduced toughness and increased susceptibility to cracking. Preheating allows for the transformation of these microstructures into more desirable forms, enhancing the mechanical properties of the weld.
What Preheat Temperature is Required?
The determination of preheat temperature in welding is typically guided by welding codes, which establish minimum temperature requirements. However, these minimum values may not always be sufficient to prevent cracking in all scenarios.
For instance, when constructing a beam-to-column connection using low-hydrogen electrodes made of ASTM A572-Gr50 and A36 jumbo sections (with thickness ranging from 4 to 5 inches), the specified minimum prequalified preheat temperature is 225°F (107°C) according to AWS D1.1-96, Table 3.2.
Nevertheless, when performing butt splices in jumbo sections, it is recommended to exceed the minimum prequalified temperature and adhere to the preheat temperature specified by AISC for such connections, which is 350°F (175°C) as stated in AISC LRFD J2.8. This cautious approach acknowledges the possibility that the minimum preheat requirements set by AWS D1.1 might not be sufficient for these highly constrained joints.
How is Preheat Applied?
When deciding on the preheating method, several factors need to be taken into account, including the thickness of the material, the size of the weldment, and the available heating equipment.
For instance, smaller production assemblies can be effectively heated using a furnace, while larger structural components often necessitate multiple heating torches, electrical strip heaters, or induction and radiant heaters.
When it comes to preheating carbon steels, a high degree of precision is generally not essential. While it is important to reach the minimum required temperature, exceeding it by approximately 100°F (40°C) is acceptable. However, this approach is not applicable to quenched and tempered (Q&T) steels.
Excessive heating of Q&T steels during welding can have adverse effects on the heat-affected zone. Consequently, it is crucial to establish and strictly adhere to both maximum and minimum preheat temperature limits for Q&T steels.
Determining the Necessary Preheat Temperature
In situations where welding codes do not provide specific guidelines for preheat temperature, determining an appropriate preheat temperature can be challenging. However, AWS D1.1, Annex XI: “Guideline on Alternative Methods for Determining Preheat,” offers two procedures for establishing preheat temperature based on laboratory cracking tests. These methods are particularly useful when there is an increased risk of cracking due to factors such as composition, restraint, hydrogen level, or lower welding heat input.
The first method outlined in Annex XI of AWS D1.1-96 is called heat-affected zone (HAZ) hardness control. This method, applicable only to fillet welds, operates under the assumption that if the hardness of the HAZ is kept below a critical value, cracking will not occur. This is achieved by controlling the cooling rate. The critical cooling rate can be correlated to the carbon equivalent of the steel, which is calculated using the formula:
CE = C + ((Mn + Si)/6) + ((Cr + Mo + V)/5) + ((Ni + Cu)/15)
Based on the critical cooling rate, a minimum preheat temperature can be determined. However, it’s important to note that while this method can establish a preheat level, its main value lies in determining the minimum heat input (and consequently the minimum weld size) required to prevent excessive hardening (AWS D1.1, Annex XI, paragraph 3.4).
The second method, known as the hydrogen control method, relies on the assumption that cracking will not occur if the amount of hydrogen remaining in the joint after it has cooled down to approximately 120°F (50°C) does not exceed a critical value.
This critical value is dependent on the steel composition and restraint. This method is particularly useful for high-strength, low-alloy steels with high hardenability. However, the calculated preheat temperature may be overly conservative for carbon steels.
The hydrogen control method involves three basic steps:
- Calculate a composition parameter similar to the carbon equivalent.
- Calculate a susceptibility index based on the composition parameter and the diffusible hydrogen content of the filler metal.
- Determine the minimum preheat temperature based on the restraint level, material thickness, and susceptibility index.
By following these steps, an appropriate preheat temperature can be determined using the hydrogen control method.
How is Preheat Applied?
When heating the joint to be welded, the AWS D1.1 code requires that the minimum preheat temperature be established at a distance that is at least equal to the thickness of the thickest member, but not less than 3 in. (75 mm) in all directions from the point of welding.
To ensure that the full material volume surrounding the joint is heated, it is recommended practice to heat the entire area within a larger radius, typically 6 to 12 inches (150 to 300 mm) beyond the immediate weld zone. This helps to minimize temperature gradients and ensures consistent preheating throughout the joint.
The preheating process should be carried out gradually to avoid thermal shock and potential cracking. It is recommended to increase the temperature at a rate of approximately 100°F (40°C) per hour until the desired preheat temperature is reached. Once the preheating temperature is achieved, it should be maintained throughout the welding process to prevent rapid cooling and potential cracking.
Monitoring and controlling the preheat temperature is crucial for ensuring the quality of the weld. Temperature-indicating crayons or temperature-measuring devices, such as infrared thermometers or thermocouples, can be used to measure and verify the preheat temperature. Regular checks should be performed to ensure that the preheat temperature remains within the specified range.
Conclusion
In conclusion, the required preheat temperature for welding depends on various factors, including the welding code, material type, thickness, and joint configuration. Welding codes often provide minimum preheat temperature requirements, but additional considerations may be needed for specific applications.
Methods for determining the necessary preheat temperature include HAZ hardness control and hydrogen control. It is important to apply preheat gradually, maintain the temperature throughout welding, and monitor it to ensure compliance with the specified requirements.