What is Golden Joint in Piping?
A “golden joint” pertains to a welded joint that typically serves as the ultimate connection between existing piping and newly installed piping. This specific joint is exempted from pressure testing. Instead of undergoing a pressure test, non-destructive examination (NDE) methods are employed.
The significance of a golden joint lies in the fact that it requires highly skilled welders. This preference for proficient welders ensures the utmost quality and integrity of the joint, considering the absence of a pressure test.
— A “Golden Joint” refers to a tie-in joint commonly found in the final stages of piping installation. This particular joint cannot undergo a hydrostatic test. —-
Golden Joint meaning
A “golden weld” or “golden joint” refers to a specific weld that cannot undergo hydrostatic testing due to various reasons, such as being the final weld on-site, the presence of refractory material behind the weld, or other similar circumstances.
As a result, this weld is subjected to comprehensive non-destructive testing (NDT), typically utilizing multiple techniques such as ultrasonic testing (UT), radiographic testing (RT), magnetic particle testing (MT), liquid penetrant testing (PT), and more.
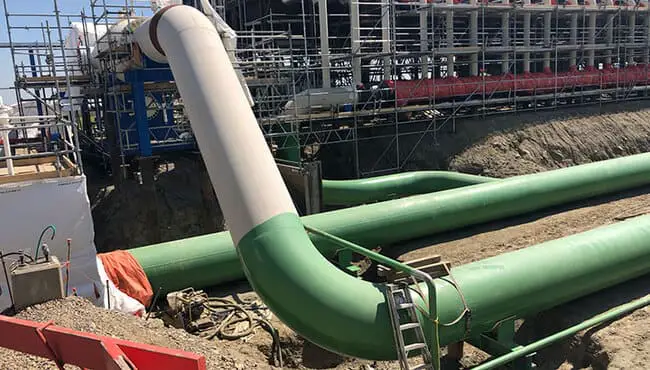
The term “golden” is associated with this weld due to the significant cost involved in conducting multiple rounds of 100% NDT inspections. The extensive inspection process ensures the weld’s quality and integrity without relying on hydrostatic testing.
The term “golden” reflects the meticulous attention and resources dedicated to scrutinizing the weld through various NDT methods, emphasizing its critical nature and the importance of achieving a flawless outcome.
By labeling it as a “golden weld” or “golden joint,” it highlights the exceptional level of scrutiny, precision, and investment required to ensure the weld’s reliability and performance, compensating for the absence of hydrostatic testing.
NDT Requirements for Golden Joints
In piping, “Golden Joints” are critical welds that cannot undergo hydrostatic testing due to various reasons such as being the final weld on-site or the presence of refractory material behind the joint. Consequently, non-destructive testing (NDT) becomes crucial to validate the quality and integrity of these joints.
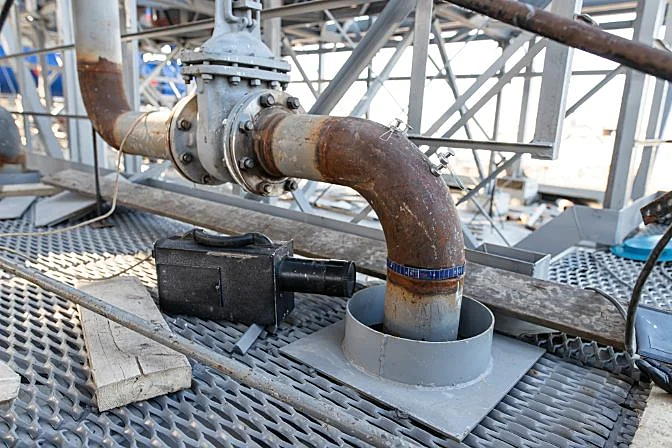
Following the completion of post-weld heat treatment (PWHT), NDT is performed on golden joints based on the specific requirements dictated by the piping class, thickness, and service limitations. The purpose of NDT is to detect any potential defects or flaws that could compromise the performance and safety of the joint.
Several NDT tests are commonly employed for golden piping joints:
- Radiographic Testing (RT): This method utilizes X-rays or gamma rays to inspect the weld for internal defects, cracks, or inclusions. It follows the guidelines outlined in Article 2 of ASME BPVC Code section V.
- Ultrasonic Testing (UT): UT employs high-frequency sound waves to evaluate the weld’s internal structure, detecting any flaws or discontinuities. It complies with the guidelines provided in Article 5 of ASME BPVC Code section V.
- Magnetic Particle Testing (MPT): MPT utilizes magnetic fields and iron particles to identify surface and near-surface defects such as cracks or discontinuities. It adheres to the guidelines outlined in Article 7 of ASME BPVC Code section V.
- Dye Penetration Test (DPT): DPT involves applying a liquid dye to the weld surface, allowing it to penetrate any surface-breaking defects. Excess dye is removed, and a developer is applied to make the indications visible. It follows the guidelines specified in Article 6 of ASME BPVC Code section V.
Golden Joint in Pipeline- Key points
- a) A Golden Joint in piping refers to a specific type of welding performed on-site during tie-in or balance welding processes. These joints are typically not subjected to hydrostatic testing due to practical constraints, such as long pipe lengths. Instead, they undergo 100% radiographic testing (RT) or ultrasonic testing (UT) as non-destructive examination (NDT) methods to ensure their quality and integrity.
- b) While there is no specific code dedicated to Golden Joints, many companies adopt the practice of performing a “golden weld” by eliminating the hydrostatic test. Instead, they rely on 100% NDT inspections to validate the weld’s quality and integrity.
- c) ASME 31.4 permits a “waiver” of hydrostatic testing for tie-in welds between two sections of piping if these welds have undergone 100% NDT inspections. This provision can be found in Section 437.1.4 (b) of the ASME B31.4 2002 Edition, which outlines the guidelines for testing tie-ins.
Golden Joint in ASME B31.3 Code
the term “Golden welds” is an industry slang and may not be explicitly mentioned in codes. However, the concept of critical welds or closure welds can be found in the industry standards. In the case of B31.3:2006, para 345.2.3 (c) addresses closure welds.
For closure welds, the requirements include in-process inspection as outlined in para 344.7 of B31.3:2006. This involves conducting inspections during the welding process. Additionally, radiographic testing (RT) or ultrasonic testing (UT) is typically required for closure welds.
It is important to generate suitable reports for all the steps mentioned in para 344.7.1 to meet the requirements of the purchaser or client.
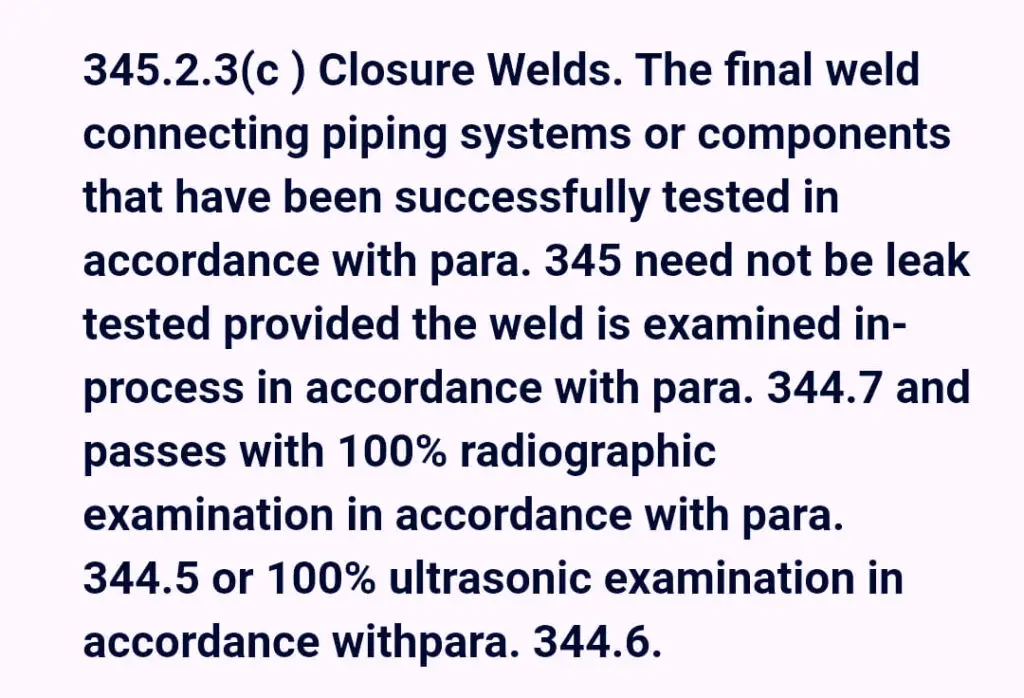
API 570 Golden Joint Inspection
First of all, as mentioned earlier- There is no Golden Joint word in welding codes. The right term is- Closure Weld. Regarding, API 570 Closure joint in piping inspection requirements, following are the requirements-
In cases where it is impractical to conduct a pressure test on a final closure weld that connects a new or replacement section of piping to an existing system, the following requirements must be met:
- The new or replacement piping must undergo a pressure test to ensure its integrity.
- The closure weld must be a full penetration butt-weld between a weld neck flange and a standard piping component or straight sections of pipe that have the same diameter, thickness, and axial alignment (without miter cuts). Alternatively, slip-on flanges can be used for design cases up to Class 150 and 500°F (260°C), or socket welded flanges or socket welded unions can be used for sizes up to NPS 2 and design cases up to Class 150 and 500°F (260°C). A spacer or other means should be employed to create a minimum 1/16 inch (1.6 mm) gap for socket welding, which must comply with ASME B31.3 standards and consist of a minimum of two passes.
- Any final closure butt-weld must undergo 100 percent radiographic quality testing. Alternatively, angle beam ultrasonic flaw detection may be used if appropriate acceptance criteria have been established.
- Magnetic particle testing (MT) or liquid penetrant testing (PT) must be performed on the root pass and the completed weld for butt-welds, and on the completed weld for fillet welds.