Crater cracks are welding defects that can occur when the weld pool cools too quickly. This article explores the causes of crater cracks and provides insights into preventing and addressing this common issue in welding.
“Crater cracks are welding defects characterized by the formation of cracks within the weld crater, resulting from the rapid cooling and shrinkage of the weld metal. “
What are Crater Cracks in Welding?
Crater cracks are welding defects that arise when the weld pool cools rapidly, resulting in the formation of cracks.
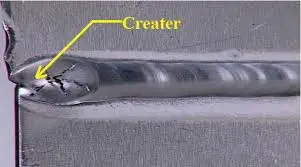
Insufficient heat input, excessive wind exposure, and fast welding speed are the primary factors contributing to the occurrence of crater cracks.
Causes of Crater Cracks in Welding
Insufficient Heat Input:
Insufficient heat input can lead to rapid cooling of the weld pool, causing it to solidify too quickly and create cracks. This may occur due to inadequate power, improper machine settings, or other factors impeding proper heat transfer.
It is essential to ensure that the welding equipment is appropriately calibrated and that the power and heat input levels are adjusted correctly for the specific welding application.
Excessive Welding Speed:
Welding too fast does not allow enough time for the weld pool to cool adequately. The rapid cooling can result in the formation of cracks as the weld solidifies.
It is crucial to find the optimal speed that allows for sufficient heat dissipation, ensuring proper solidification of the weld without excessive cooling.
Wind Exposure:
Wind blowing onto the weld pool can accelerate the cooling process, causing the formation of crater cracks. Proper shielding of the weld area from wind or the use of windbreaks can help minimize this risk.
Additionally, positioning the welding operation in a controlled environment, such as a dedicated welding booth or using suitable welding curtains, can provide additional protection from wind interference.
Crater Crack in MIG Welding
When a weld is completed and the wire feed is abruptly stopped, it can lead to the formation of a shrinkage crater. This article discusses the consequences of crater formation, such as surface depressions and elongated pores, as well as the potential for shrinkage stresses to cause hot short or crater cracks. Additionally, various methods of eliminating this defect are explored.
Shrinkage Craters and Surface Depressions:
If the weld pool is small, the resulting crater may manifest as a shallow depression on the weld surface. However, in larger weld pools, the crater can extend deeper into the weld and form an elongated pore known as piping porosity. These surface irregularities can compromise the structural integrity of the weld and must be prevented.
Shrinkage Stresses and Crater Cracks:
As the weld continues to cool and contract, the associated shrinkage stresses can induce the formation of hot short or crater cracks. These cracks can weaken the weld and increase the risk of failure. It is crucial to avoid any form of cracking in welding applications.
Methods to Eliminate Crater Defects:
Several methods can be employed to prevent and eliminate crater defects:
- Use of Run-off Tabs:
By terminating the weld on run-off tabs, which are subsequently removed, the abrupt cessation of the wire feed can be avoided. This allows for a more controlled solidification of the weld pool, reducing the likelihood of crater formation. - Increasing Travel Speed:
Skillful manipulation of the travel speed just before releasing the trigger can cause the weld pool to tail out over a distance. This technique requires expertise on the part of the welder but can help minimize craters and ensure smoother weld surfaces. - Controlled Stops and Starts:
Making a small number of brief stops and starts into the crater as the weld cools can add filler metal to the depression, effectively filling it. This method requires precision and careful timing to prevent excessive heat input or distortion. - Gradual Ramp-down of Wire Feed and Current:
By gradually reducing the wire feed speed and welding current as the trigger on the torch is released, the crater is fed with smaller amounts of molten filler metal. This progressive filling and elimination of the crater is facilitated by modern welding equipment and is the preferred method to prevent piping porosity and crater cracks.
Prevention of Crater Cracks in Welding
To prevent crater cracks from occurring, several measures can be taken:
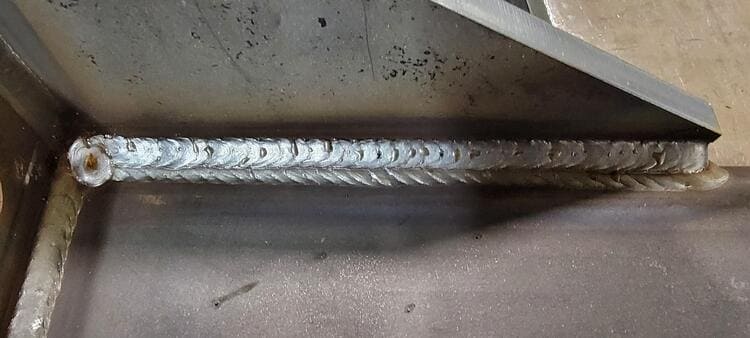
Sufficient Power and Heat Input:
Ensuring that the welder has enough power and heat input is crucial. Adequate amperage in arc welding is necessary to maintain the optimal temperature and prevent rapid cooling.
Proper machine setup and regular maintenance are essential to ensure consistent power output.
Optimal Welding Speed:
Finding the right balance between welding speed and cooling time is essential. Adjusting the welding speed to allow for proper cooling of the weld pool can help prevent the formation of crater cracks.
It is important to consider factors such as the material being welded, the joint configuration, and the specific welding process being used when determining the appropriate speed.
Managing Wind Conditions:
Being mindful of wind conditions and taking necessary precautions to shield the weld pool from excessive wind exposure can help prevent rapid cooling and subsequent cracking.
This can include the use of windbreaks, welding screens, or relocating the welding operation to a more controlled environment whenever possible.
Handling Crater Cracks in Welds
If a weld exhibits crater cracks, it is important to address the issue promptly:
Inspection by a Qualified Welding Inspector:
Having a qualified welding inspector inspect the weld is crucial to identify and assess the extent of the crater cracks accurately.
They can provide expert guidance on the appropriate repair methods and ensure that the weld meets the required standards.
Proper Repair:
Crater cracks can usually be repaired by rewelding the affected area. However, it is vital to address the root cause of the problem to prevent future occurrences.
This may involve adjusting welding parameters, improving heat control, or implementing other measures to minimize rapid cooling.