CJP and PJP Weld Symbols
Weld symbols contain a wealth of information for fabricators and welders. Two symbols that give important clues about the weld process are “CJP” and “PJP”. Let’s decode what these cryptic markings mean.
Weld symbols may appear illogical initially, but once understood, they beautifully and concisely communicate essential welding data.
What is a Complete Penetration Weld-CJP Weld?
CJP means “complete joint penetration”. This tells you that the weld must fully penetrate through the total thickness of the joint being welded.
👉 CJP welds are designed to fuse both materials completely with no unfused areas left.
The Complete Joint Penetration (CJP) groove weld is a type of weld where the groove extends entirely through the thickness of the joined components. The main objective of using CJP groove welds is to ensure that the structural components can carry the full load effectively.
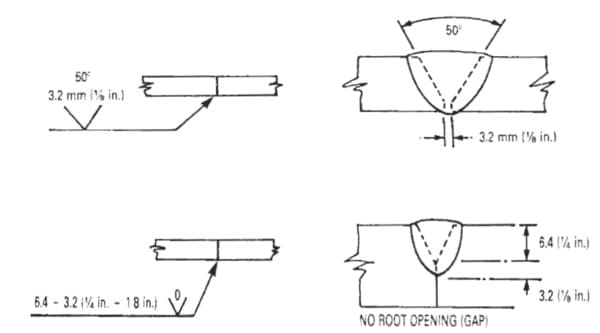
Typically, CJP welds require specific edge preparations to achieve the desired weld quality. While it is important to utilize CJP welds when necessary, it is advisable to limit their usage to a minimum.
How do you achieve complete penetration in a CJP Weld?
CJP welds typically require specialized processes like laser or electron beam welding. The high energy density of these methods ensures full fusion.
To achieve complete penetration in welding, several factors need to be considered and controlled:
- Joint Design: The joint design plays a critical role in achieving complete penetration. The joint configuration, including the groove angle, root opening, and bevel angle, should be properly selected to allow for adequate access and fusion of the weld metal throughout the joint thickness.
- Welding Process: The choice of welding process can significantly impact the ability to achieve complete penetration. Processes such as gas tungsten arc welding (GTAW/TIG), gas metal arc welding (GMAW/MIG), or shielded metal arc welding (SMAW/stick) can be used. Each process has its own characteristics and considerations, such as heat input, welding speed, and control of the molten weld pool.
- Welding Parameters: Proper control of welding parameters is essential for achieving complete penetration. Variables such as welding current, voltage, travel speed, and filler material selection should be optimized based on the joint configuration, material properties, and desired penetration depth.
- Joint Preparation and Fit-Up: Adequate joint preparation, including cleaning and removal of contaminants, is important to ensure proper fusion and penetration. The fit-up between the components being joined should be precise, with minimal gaps or misalignment, to facilitate proper fusion throughout the joint thickness.
- Welding Technique: The welding technique employed can influence the attainment of complete penetration. Maintaining a suitable arc length, controlling the weld pool shape and size, and properly manipulating the welding torch or electrode can help ensure adequate fusion and penetration.
- Inspection and Quality Control: Regular inspection and quality control measures, including visual examination, non-destructive testing (NDT), and destructive testing, should be carried out to verify the achieved penetration and ensure compliance with specified requirements.
What is a PJP Weld?
PJP stands for “partial joint penetration”. As the name implies, partial penetration means the weld does not extend fully through the thickness of the metals.
👉 In PJP Weld, A portion of the joint thickness remains unfused.
Partial penetration welds are common with manual processes like GMAW or SMAW welding. Welders control the depth of penetration via technique and parameters.
CJP Weld Symbol
As a welder, you’re probably used to deciphering all kinds of cryptic markings and symbols. One symbol that carries a lot of significance is “CJP.” Let’s shed some light on what this little marking means.
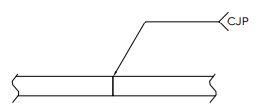
When employing a CJP groove weld or a PJP groove weld, it is recommended that the designer avoids providing explicit details about the groove configuration or specifying the symbol for a particular weld type, such as a double-V-groove or square-groove.
Below CJP Weld symbols explain different methods to achieve a complete penetration CJP Weld mainly by using a:
- Burn through weld,
- Consumable Insert
- A Plug Weld
- A Removable backing,
- A Permanent Backing.

Instead, the weld arrow should be directed towards the joint location, and the designation of CJP or PJP should be indicated, as demonstrated in the accompanying figures.
A CJP Weld symbol is identified by placing term CJP in the welding symbol tail section as shown below:
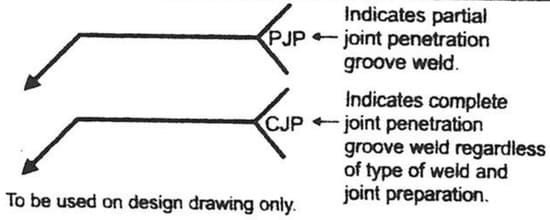
PJP Weld Symbol
The PJP (Partial Joint Penetration) weld symbol is used to represent a specific type of weld joint where the weld metal does not fully penetrate the joint thickness.
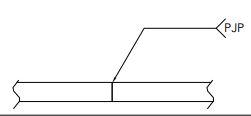
Unlike the CJP weld symbol, which indicates complete joint penetration, the PJP weld symbol denotes that only a partial penetration is required for the weld joint.

Why is complete penetration so important?
Partial penetration defects in a weld can result in weak spots that act as stress risers. This leads to cracking or premature failure when the welded part is placed into service. No bueno!
So when you see CJP on a welding symbol or drawing, you know that meticulous process control is needed to avoid defects and deliver full fusion. It’s a marker that alerts welders to a critical quality expectation.
Complete penetration in welding is crucial for several reasons:
- Load-Carrying Capacity: A weld joint with complete penetration ensures that the entire cross-section of the joint is fused, resulting in maximum strength and load-carrying capacity. It allows the joined components to distribute and transfer stresses effectively, ensuring structural integrity.
- Joint Strength: Complete penetration provides a continuous and uniform weld profile throughout the joint. This results in improved joint strength and resistance to fatigue, fracture, and failure under applied loads.
- Leakage Prevention: In applications involving pressure containment or fluid flow, such as pipelines or pressure vessels, complete penetration is essential to prevent leaks. A fully penetrated weld joint ensures a tight seal and prevents the escape of fluids or gases.
- Weld Quality and Durability: Welds with complete penetration exhibit better metallurgical properties, such as homogeneity and uniform grain structure, which contribute to enhanced durability and resistance to corrosion.
- Design Intent: In many engineering designs, the structural integrity and performance of the joint depend on the assumption of complete penetration. Deviating from this design requirement may compromise the intended functionality and safety of the structure.
However, it’s important to note that not all weld joints require complete penetration. There are instances where partial joint penetration or specific groove designs are acceptable based on engineering considerations, material thickness, and joint requirements.
In such cases, appropriate weld symbols and specifications are used to indicate the desired level of penetration.
FAQs on Complete Joint Penetration (CJP) Welds:
- What is a Complete Joint Penetration (CJP) weld?
- A Complete Joint Penetration (CJP) weld is a type of weld where the joint is fully penetrated, meaning that the weld extends through the entire thickness of the joint.
- How is a Complete Joint Penetration weld different from other types of welds?
- A Complete Joint Penetration weld differs from other types of welds, such as partial penetration welds, as it ensures full fusion and penetration through the entire joint thickness.
- When is a Complete Joint Penetration weld necessary?
- Complete Joint Penetration welds are typically required in applications where maximum strength and structural integrity are essential, such as in critical load-bearing structures or high-pressure vessels.
- What are the advantages of achieving Complete Joint Penetration in a weld?
- Achieving Complete Joint Penetration provides a weld joint with excellent strength, improved resistance to fatigue, and enhanced overall integrity. It ensures that the welded structure can withstand the intended loads and stresses.
- What are the challenges in achieving Complete Joint Penetration welds?
- Achieving Complete Joint Penetration can be challenging due to factors such as joint preparation, fit-up accuracy, welding technique, and control of heat input. It requires careful planning, skillful execution, and adherence to proper welding procedures.
- How can I ensure proper penetration in a CJP weld?
- Proper penetration in a CJP weld can be ensured by correctly preparing the joint edges, selecting appropriate welding parameters, using proper welding techniques, and ensuring proper alignment and fit-up of the workpieces.
- What welding processes are commonly used for Complete Joint Penetration welds?
- Welding processes such as Shielded Metal Arc Welding (SMAW), Gas Metal Arc Welding (GMAW), Flux-Cored Arc Welding (FCAW), and Gas Tungsten Arc Welding (GTAW) are commonly used for achieving Complete Joint Penetration.
- Are there any specific welding codes or standards that govern CJP welds?
- Yes, there are welding codes and standards, such as those provided by the American Welding Society (AWS) and other regulatory bodies, that provide guidelines and requirements for achieving and inspecting Complete Joint Penetration welds.
- Can Complete Joint Penetration welds be achieved on all types of materials?
- Yes, Complete Joint Penetration welds can be achieved on various types of materials, including metals like steel, aluminum, and stainless steel, as well as alloys and other weldable materials.
- What inspection and testing methods are used to verify the quality of CJP welds?
- Various inspection and testing methods, such as visual inspection, radiographic testing (X-ray or gamma-ray), ultrasonic testing, or magnetic particle testing, can be used to verify the quality and integrity of Complete Joint Penetration welds.
FAQs on Partial Joint Penetration (PJP) Welds:
- What is a Partial Joint Penetration (PJP) weld?
- A Partial Joint Penetration (PJP) weld is a type of weld where the joint is partially penetrated, meaning that the weld does not extend through the entire thickness of the joint.
- How is a Partial Joint Penetration weld different from other types of welds?
- A Partial Joint Penetration weld differs from Complete Joint Penetration welds as it does not fully penetrate the joint. It is often used when complete penetration is not necessary or when it is not practical or cost-effective to achieve.
- When is a Partial Joint Penetration weld used?
- Partial Joint Penetration welds are commonly used in non-critical applications or situations where full penetration is not required, such as in non-load-bearing structures or decorative welds.
- What are the advantages of using Partial Joint Penetration welds?
- Partial Joint Penetration welds can offer advantages such as reduced heat input, faster welding speeds, and improved cost-effectiveness compared to achieving complete penetration. They are often easier to execute and can still provide sufficient strength for certain applications.
- What are the limitations of Partial Joint Penetration welds?
- Partial Joint Penetration welds may have reduced strength, lower resistance to fatigue, and decreased load-bearing capacity compared to Complete Joint Penetration welds. They may not be suitable for critical load-bearing structures or applications requiring maximum joint integrity.
- How is a PJP weld prepared and executed?
- In a PJP weld, the joint edges are typically prepared with a bevel or groove, and the weld is deposited into the prepared groove. The weld may not extend through the entire thickness of the joint, but it is still required to achieve adequate fusion and strength.
- Are there any specific welding codes or standards that govern PJP welds?
- Different welding codes and standards may provide guidelines and requirements for Partial Joint Penetration welds based on the specific application, materialrequirements, and industry standards. It is important to consult the relevant codes and standards applicable to the specific project.
- Can Partial Joint Penetration welds be used in load-bearing applications?
- Partial Joint Penetration welds can be used in certain load-bearing applications, depending on the design requirements and structural considerations. However, it is crucial to ensure that the weld joint’s strength and integrity are sufficient to withstand the anticipated loads and stresses.
- Are there any specific inspection requirements for PJP welds?
- Similar to other types of welds, PJP welds may undergo inspection and testing to verify their quality and integrity. The inspection methods can include visual inspection, radiographic testing, ultrasonic testing, or other appropriate methods based on the specific project requirements and applicable standards.
- How does the choice of welding process affect the quality of PJP welds?
- The choice of welding process can impact the quality of PJP welds. Different welding processes have varying characteristics, heat input, and deposition rates, which can affect the weld penetration, fusion, and overall quality of the joint. It is important to select a welding process suitable for the material, joint design, and project requirements to achieve satisfactory PJP welds.