Zigzag welding symbol
have come across various symbols that play a crucial role in our craft. One symbol that stands out is the zigzag welding symbol, or what we commonly refer to as the zigzag weld or intermittent weld.
Understanding the zigzag welding symbol is essential for welders like myself, as it allows us to accurately interpret and execute welds according to the specified requirements.
In this article, I will share my insights into the concept of the zigzag welding symbol, explore its features, and highlight its significance within the welding industry.
What is a ZigZag Weld?
A ZigZag Weld, also known as a skip weld or staggered intermittent weld, refers to a specific welding technique where intermittent welds are applied to one or both sides of a joint without following a specific spacing pattern. In this method, the weld increments are made without strict adherence to predetermined spacing intervals.
“Zigzag weld is a non-standard term for skip weld or staggered intermittent weld.”

This technique allows for flexibility in the welding process, as the welder has the freedom to adjust the spacing between weld increments based on the specific requirements of the joint. By disregarding strict spacing guidelines, the welder can adapt the welding pattern to accommodate variations in the joint geometry, material thickness, or other factors that may influence the welding process.
Alternatively, a ZigZag Weld can also refer to an intermittent weld on both sides of a joint, where the weld increments on one side are alternated with respect to those on the other side. This further enhances the strength and stability of the joint by distributing the weld increments in a staggered manner.
The use of ZigZag Welds provides several benefits. It allows for better control over heat input, reduces distortion, and helps distribute the welding stresses more evenly across the joint. Additionally, this welding technique can enhance the overall appearance of the weld by creating an aesthetically pleasing zigzag pattern.
Zigzag Welding Symbol meaning
The Zigzag Welding Symbol is a graphical representation used in welding design and engineering to convey specific instructions and requirements for welders and inspectors. The symbol consists of a series of connected zigzag lines placed below a horizontal reference line on a welding drawing.
The primary meaning of the Zigzag Welding Symbol is to indicate that a continuous or intermittent fillet weld is required along the length of the joint. The zigzag lines within the symbol represent the path that the weld bead should follow during the welding process. They illustrate the desired weld pattern, which may consist of alternating peaks and valleys, resembling a zigzag shape.
The Zigzag Welding Symbol also provides additional information, such as the length of each weld segment and the pitch (spacing) between them. These specifications are typically indicated on the right side of the symbol. The length of each segment is denoted, followed by a hyphen, and then the pitch measurement, which represents the center-to-center distance between consecutive segments.
Zigzag Welding Symbol
The Zigzag Welding Symbol encompasses two main types:
- Staggered intermittent weld and
- Chain intermittent weld.
When a continuous weld is not required, welders often apply an intermittent weld technique, leaving gaps between the termination of one weld and the start of the next. These individual weld sections are commonly referred to as weld segments or skip welds in the industry.
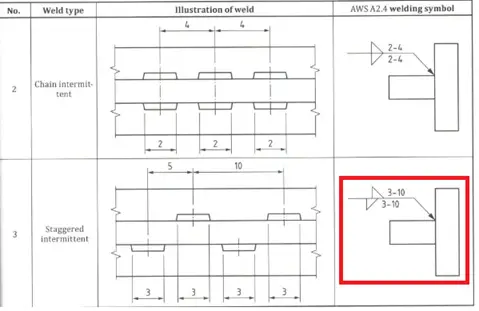
In the case of an intermittent weld, specific call-outs are made regarding the length of each weld segment and the pitch, or spacing, between them. These specifications are typically indicated on the right side of the welding symbol. The length of each segment is denoted, followed by a hyphen, and then the pitch measurement, which represents the center-to-center distance between consecutive segments.

In situations where intermittent welds are applied on both sides of the joint, it is referred to as chain intermittent welding. This technique involves alternating weld segments on one side with respect to those on the other side, creating a chain-like pattern. Chain intermittent welding provides added strength and stability to the joint while maintaining intermittent weld characteristics.
Advantages of Ziazag weld
Zigzag welds, or intermittent welds, offer several advantages in welding applications. Let’s explore some of these benefits:
- Reduced Distortion: Zigzag welds help minimize distortion in the welded components. By intentionally introducing gaps between the weld segments, the localized heat input is reduced, resulting in less overall distortion of the material. This is particularly beneficial when welding thin or heat-sensitive materials.
- Stress Distribution: Intermittent welds distribute welding stresses more evenly across the joint. The gaps between weld segments act as stress relief points, preventing the concentration of stress in a single area. This can improve the overall strength and durability of the joint.
- Improved Heat Control: Zigzag welds allow for better control over heat input during the welding process. By adjusting the length of each weld segment and the spacing between them, welders can effectively manage the heat generated. This is especially useful when welding materials with varying thicknesses or when working on complex joint configurations.
- Cost Savings: Intermittent welds can result in cost savings in certain applications. Since the weld segments are not continuous, less filler material and welding consumables are required compared to a continuous weld. This can lead to reduced material and labor costs, making intermittent welds a cost-effective option.
- Aesthetics: Zigzag welds can offer improved aesthetics in certain applications. The intermittent pattern creates a visually appealing zigzag or chain-like pattern on the surface of the weld, which can be desirable in decorative or architectural welding projects.
- Flexibility: Intermittent welds provide flexibility in the welding process. Welders can adjust the length of each segment and the spacing between them to accommodate variations in joint geometry, material thickness, or other factors.