What is Pulse Transfer mode in MIG Welding?
In the pulsed-arc metal transfer mode (GMAW-P), the welding current is pulsed, and argon is typically the dominant gas in the shielding gas mixture. Figure below provides a visual representation of the current behavior in this mode.
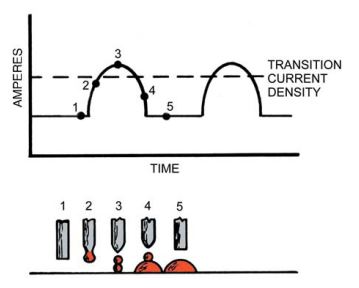
- In Position 1, a low-background current is applied, leading to the formation of a small globule on the electrode.
- In Position 2, a current pulse is on the verge of separating the globule from the electrode.
- In Position 3, the current has pulsed above the transition current density, resulting in the transfer of the droplet in the spray metal transfer mode. The spray arc also generates heat, which facilitates fusion.
- Positions 4 and 5 show the current density returning to the background level.
Advantages of the Pulsed-Arc Mode
The pulsed-arc mode offers several advantages, including:
- Option for larger electrode sizes: The pulsed-arc mode allows for the use of larger electrode sizes, providing flexibility in welding applications.
- Increased process productivity: This mode enhances process productivity due to its ability to deliver higher deposition rates and faster welding speeds.
- Enhanced fusion with greater base metal mass: Compared to the short-circuiting mode, the pulsed-arc mode enables improved fusion by allowing for greater interaction between the electrode and the base metal, particularly in applications involving a larger base metal mass.
- Suitability for all positions: The pulsed-arc mode can be utilized in various welding positions, offering versatility in different welding scenarios.
Considerations and Equipment
It’s important to note that GMAW pulsed-arc equipment is considerably more expensive than equipment used for other arc modes.
Additionally, the proper adjustment of pulsed-arc background and peaking current amplitudes and durations is crucial, depending on the electrode alloy type and size used in conjunction with the shielding gas.
Some manufacturers provide synergic systems with inverter power sources, and certain pulsed-arc systems incorporate microprocessor controls to synchronize variables.
These systems may include factory preset program options, and adjustments to the preset parameters can be made to optimize performance for specific applications.
Buried-Arc and High-Deposition-Rate Modes
The buried-arc and high-deposition-rate modes exhibit the highest current densities among metal transfer modes. These modes can exceed 300,000 A/in.2 (465 A/mm2) of the electrode cross-sectional area.
At such densities, a 0.045 in. (1 mm) electrode feeds at approximately 1500 in./min (38 meters [m]/min). The buried-arc mode operates at a low voltage, allowing the arc to be positioned below the metal surface.
This produces a narrow, deep weld profile with a high crown or buildup. In contrast, the high-deposition-rate mode utilizes a higher voltage, resulting in a wider weld profile with reduced crown and depth.
The buried-arc and high-deposition-rate modes are typically employed in fully mechanized or automatic gas metal arc welding processes.