Puddle weld vs Plug weld
While the term “puddle weld” may be used as a nonstandard term for an arc spot weld or plug weld, it is more accurate to refer to a specific weld joint as a plug weld when following standard welding terminology and drawings.
In this post I have covered, What is Puddle Weld & plug weld, their features and differences.
What is a Puddle Weld?
In standard welding terminology, the term “puddle weld” is not commonly used. However, in some contexts, “puddle weld” may refer to a weld made by depositing molten weld metal in the form of a small circular or oval-shaped puddle.
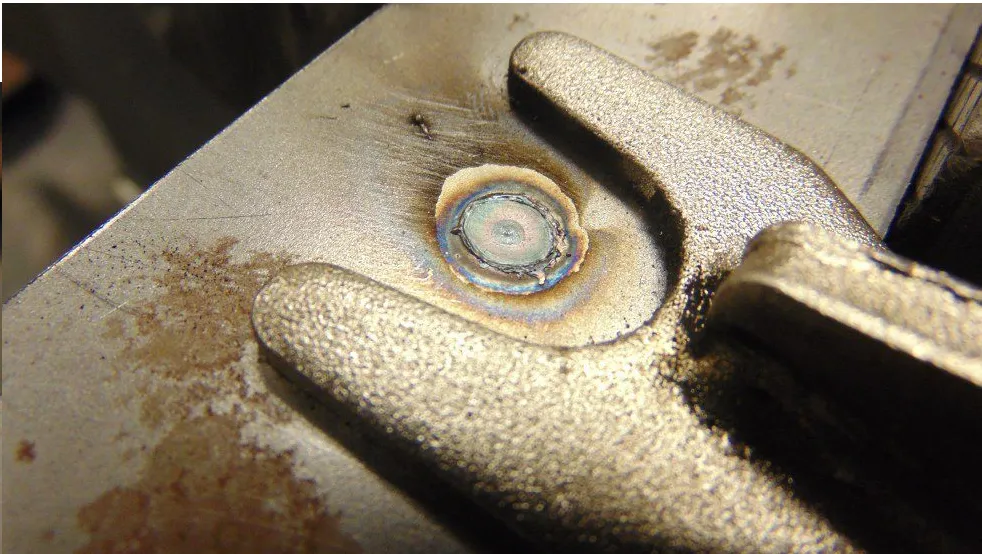
During the welding process, an arc or heat source is used to melt the base metal and filler material, forming a molten pool or puddle. The welder manipulates the puddle to ensure proper fusion and penetration between the components being joined. Once the puddle solidifies, it forms a weld joint.
What is a Plug Weld?
According to AWS A3.0, a plug weld is defined as a type of weld where a hole or opening is filled by molten weld metal. The hole or opening is typically made in one of the parts being joined, and the molten metal from the welding electrode or filler material is deposited into the hole, creating a solid weld joint.
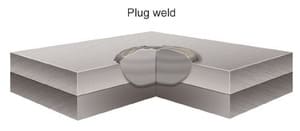
A plug weld is a weld joint created by filling a hole or slot in one metal component with weld metal to join it to another overlapping metal component.
Features and Characteristics
- Hole or Slot: A plug weld requires a hole or slot in one component, which is aligned with the corresponding area on the other component.
- Precise Fit-up: The components are accurately positioned to ensure proper alignment and fit-up of the hole or slot.
- Weld Filler: A filler metal is inserted into the hole or slot, which is melted to create the weld joint.
- Solidification: The molten metal cools and solidifies, forming a strong bond between the components.
Applications
- Automotive Industry: Plug welds are commonly used in vehicle manufacturing to join various metal components, such as body panels, brackets, and frames.
- Structural Steelwork: Plug welds are employed in the construction of steel structures, including bridges, buildings, and industrial facilities.
- Fabrication and Manufacturing: Plug welds are used in general fabrication and manufacturing processes to secure overlapping metal components.
Strength
- Plug welds can provide high-strength connections when properly executed.
- The strength of a plug weld depends on factors such as the size of the hole or slot, the type and quality of the weld filler, and the welding technique used.
- When designed and executed correctly, plug welds can distribute the load evenly across the joint, effectively transferring forces between the components.
Puddle weld vs Plug weld Differences
Puddle weld and plug weld are often used interchangeably; however, it’s important to note that “puddle weld” is a non-standard term for a plug weld. Both refer to the same welding technique where a hole or opening is filled with molten weld metal to create a solid joint between two metal components.
The term “plug weld” is widely recognized and used in various welding standards and codes, such as AWS (American Welding Society) and ASME (American Society of Mechanical Engineers). It describes the process of depositing weld metal into a prepared hole or opening, effectively “plugging” it and creating a strong bond between the two parts.
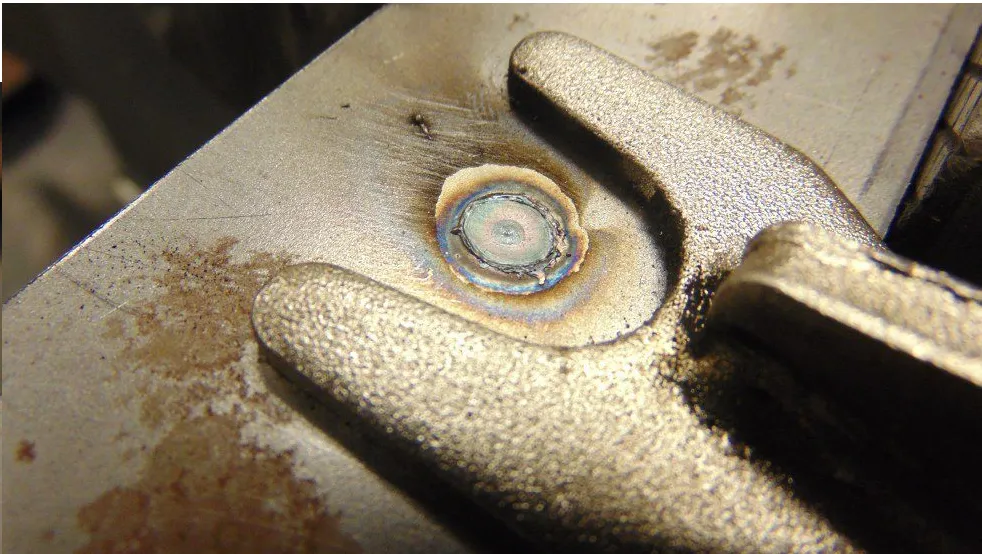
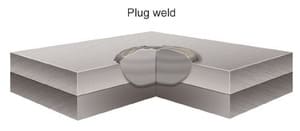
On the other hand, “puddle weld” may be used colloquially or in certain specific contexts, but it is not an officially recognized term in welding standards. It is essentially synonymous with plug weld, referring to the same welding technique and process of filling a hole with molten weld metal to achieve a secure joint.