When it comes to welding, achieving strong and flawless welds is of utmost importance for ensuring the structural integrity and reliability of the finished product.
However, there are certain welding defects that can compromise the quality of the weld joint. One such defect is known as cold lap.
In this blog post, we will delve into the concept of cold lap, its causes, effects, and most importantly, how to prevent it.
What is Cold Lap in Welding?
Cold lap is a welding defect that occurs when the weld metal fails to fuse properly with the base metal or when there is an overlap between the two metals.
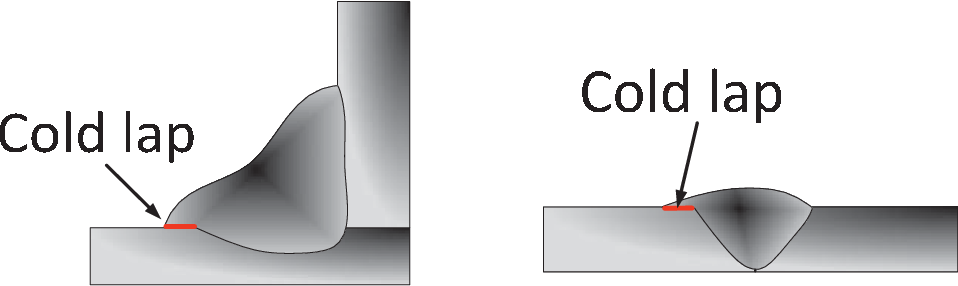
It is characterized by a visible line along the weld joint where the fusion is incomplete. Cold lap can adversely affect the strength and integrity of the weld, making it essential to identify and address this issue during the welding process.
Welding Cold Lap
Cold lap is a welding imperfection that arises when the molten metal fails to fully fuse with the cold plate surface.
This results in the formation of a crack-like defect, typically small in size, which runs parallel to the plate.
A research study has classified cold lap weld defects into three categories based on a series of tandem arc MIG/MAG welding experiments:
Spatter cold lap
This type of cold lap occurs when spatter, which refers to small droplets of molten metal expelled during welding, interferes with the fusion between the weld metal and the base metal.
The presence of spatter leads to incomplete fusion and the formation of cold lap along the weld joint.
Overlap cold lap
Overlap cold lap emerges when there is an overlap or excess deposition of weld metal on the base metal.
This excessive deposition prevents proper fusion and results in cold lap defects along the weld, parallel to the plate surface.
Spatter-overlap cold lap
The spatter-overlap cold lap defect combines elements of both spatter and overlap cold lap.
It occurs when spatter interference and excessive weld metal deposition coincide, leading to incomplete fusion and the formation of cold lap defects.
Causes of Cold Lap
Several factors can contribute to the occurrence of cold lap in welding. Incorrect welding parameters, such as inadequate heat or insufficient welding speed, can hinder proper fusion between the weld metal and base metal.
Additionally, insufficient cleaning of the metals before welding or the presence of contaminants on the welding area can also lead to cold lap. Identifying the root causes of cold lap is crucial for implementing effective preventive measures.
Preventing Cold Lap
Prevention is key when it comes to avoiding cold lap in welding. Here are some essential steps to take:
- Use the proper welding parameters: Ensure that the welding equipment is set up correctly, including the appropriate heat settings and welding speed. This will facilitate proper fusion between the weld metal and base metal.
- Maintain cleanliness: Thoroughly clean the metals before welding to eliminate any dirt, grease, or other contaminants that could hinder fusion. Proper cleaning techniques, such as wire brushing or solvent cleaning, should be employed.
- Shield the welding area: Utilize suitable shielding techniques, such as the appropriate choice of shielding gas or flux, to prevent the formation of oxide layers and ensure a clean weld area.
Repairing Cold Lap
Despite our best efforts, cold lap can occasionally occur. In such cases, it is important to address the issue promptly.
The standard method for repairing cold lap involves grinding away the defective portion of the weld, removing any impurities or incomplete fusion, and subsequently re-welding the joint using the correct welding parameters.