Arc force plays a crucial role in welding, as it involves the interaction between the welding electrode and the workpiece, resulting in the formation of a weld joint. This article aims to provide a comprehensive understanding of arc force, including its factors, application, and impact on welding quality.
Arc Force Function in a Welder
Arc Force, also referred to as “Dig” or “Arc Control,” is a welding function that operates throughout the welding process, unlike Hot Start, which only activates during ignition.
When a short circuit is detected by the welding machine, it responds by delivering a surge of current. This surge plays a vital role in stabilizing the arc, preventing it from cutting out while welding, and mitigating electrode sticking issues.
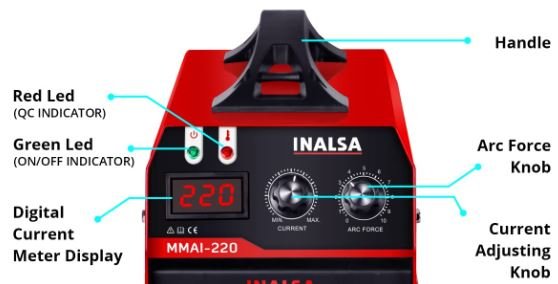
The purpose of Arc Force is to maintain a steady and uninterrupted arc by providing an additional current peak when a short circuit occurs. This feature is especially valuable in situations where the welding arc is prone to interruptions or when the electrode has a tendency to stick to the workpiece.
By incorporating Arc Force into the welding process, welders can ensure a more consistent and controlled welding operation. This dynamic control feature actively prevents arc instability and electrode sticking, resulting in improved welding quality and performance.
What is Arc Force in Welding?
The adjustment of the arc force knob modifies the shape of the volt/amp curve produced by the welding machine during shielded metal arc (SMA) welding.
A high arc force setting results in a “drooper” curve, where the amperage decreases significantly as the voltage (arc length) increases, creating a stiffer arc.
Conversely, the amperage increases substantially when the voltage decreases. High arc force is beneficial when working with thick or rusty metal, as it promotes deep joint penetration.
It is also useful for accommodating variations in joint fit-up since the amperage can be controlled by adjusting the arc length.
“Arc force, also known as arc control or dig control, refers to the additional amperage provided during low voltage conditions.”
Amperage plays a significant role in heat generation and penetration during welding. Typically, this low voltage condition is maintained at levels below 20-24 volts.
On the other hand, low arc force corresponds to a steep volt/amp curve and produces a softer arc. With low arc force, changing the arc length has minimal impact on the amperage.
This softer arc is advantageous for higher amperage welding or applications involving sheet metal or low penetration that require lower amperage. However, it is more prone to sticking to the workpiece.
Factors Influencing Arc Force:
Several factors influence the generation of arc force in welding:
- Welding Process: Different welding processes, such as shielded metal arc welding (SMAW), gas metal arc welding (GMAW), or flux-cored arc welding (FCAW), have varying arc force characteristics.
- Electrode Size and Shape: The size and shape of the electrode affect the concentration and distribution of the arc force.
- Metal Type: Different metals have specific electrical and thermal conductivity properties, which influence arc force generation.
- Welding Speed: The speed at which the weld is performed affects the heat input and, subsequently, the arc force.
Understanding these factors is essential for welders to control and optimize arc force during the welding process.
Importance of Arc Force Control:
Excessive arc force can lead to workpiece distortion or even workpiece breakage, compromising the integrity of the weld joint.
Therefore, welders must carefully control the arc force to prevent such issues. By adjusting crucial parameters, welders can ensure the optimal amount of arc force is applied during welding.
Utilizing Arc Force in Welding:
To effectively utilize arc force in welding, welders employ various techniques:
- Arc Force Setting: Welders can adjust the welding current to control the intensity of the arc force. Higher settings result in increased current and greater arc force. Finding the right arc force setting is crucial for achieving high-quality welds.
- Hot Start Technique: The hot start technique involves using high arc force at the beginning of the welding process to initiate the weld joint effectively.
By understanding these techniques and applying them appropriately, welders can harness arc force to create strong and reliable weld joints.
Arc Force Requirements for Specific Electrodes:
The arc force requirements for specific electrode types, such as 7018, 6011, and 6013, depend on the welding process, electrode characteristics, metal type, and welding speed.
Each electrode type has its own optimal arc force settings, which can be determined through experience, manufacturer recommendations, and welding standards.