What is Cap Pass in Welding?
In a completed welding joint, a cap pass refers to the final weld pass or the topmost layer of a weld joint.
“It is the last step in the welding process and is used to provide a smooth and aesthetically pleasing finish to the weld.“
The cap pass is typically performed after the root pass and any intermediate filler passes have been completed. Its primary purpose is to ensure complete fusion and proper reinforcement of the weld joint.
The welder carefully deposits the filler metal along the joint, ensuring adequate penetration and coverage.
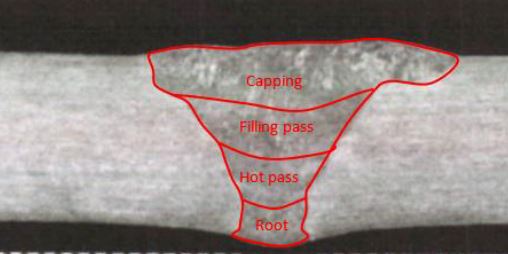
The cap pass is important not only for its visual appearance but also for its functional aspects. It helps to protect the underlying weld from environmental factors, such as corrosion or mechanical damage.
Additionally, a well-executed cap pass contributes to the overall strength and integrity of the weld.
What are the passes of weld?
In welding, the term “passes” refers to the individual weld bead layers that are deposited to complete a weld joint. Each pass contributes to the overall strength, integrity, and quality of the weld.
The number and sequence of passes required can vary depending on factors such as the type of joint, the welding process, and the thickness of the materials being welded.
Here are the main types of passes:
In the welding joint figure below:
- A- Root Run
- B- Hot Pass
- C- Filling Pass
- D- Cap Pass
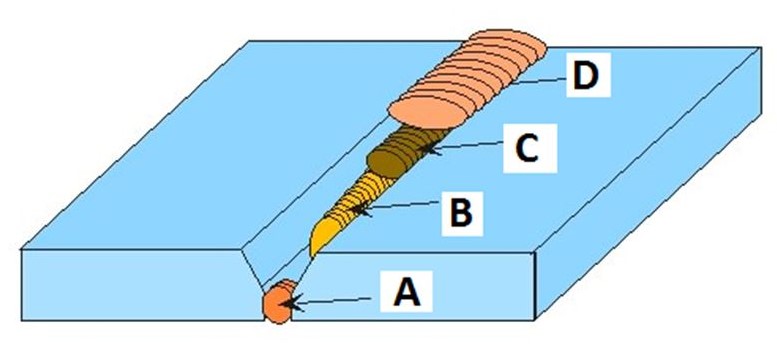
What is a Root Pass?
The root pass is the first pass deposited in the joint. It is typically done to achieve proper fusion at the root of the joint. In some cases, it may involve the use of a backing strip or a backing gas to support the root weld.
What is a Fill Pass?
The fill pass follows the root pass and is used to build up the weld by adding additional layers of filler metal. It helps to achieve the required weld size, strength, and reinforcement.
What is a Cap Pass?
The cap pass is the final pass in the welding process. It is responsible for providing a smooth and visually appealing finish to the weld joint. The cap pass is typically performed after the root and fill passes have been completed.
What is a Hot Pass?
In some welding processes, such as shielded metal arc welding (SMAW) or flux-cored arc welding (FCAW), a hot pass may be used. It is an optional pass that is applied after the root pass and helps to remove any slag or impurities and improve the overall weld quality.
What is a Cap Pass or Cover Pass?
A cover pass is an optional pass that is applied over the final weld bead to provide additional reinforcement and protection. It is often used in critical applications or when additional strength or corrosion resistance is required.
The number of passes required for a weld joint can vary depending on the welding procedure, joint design, and material thickness.
Welding procedures and standards specify the specific number and types of passes needed to ensure a sound and reliable weld.
How do you weld fill and cap passes?
To weld fill and cap passes:
- Prepare the joint and clean the surfaces.
- Choose the appropriate welding process and parameters.
- Tack weld the joint in position.
- Weld the root pass for proper fusion.
- Add fill passes to build up the weld.
- Perform the cap pass for a smooth finish.
- Inspect the weld for defects.
- Follow welding procedures and techniques for quality results.
How can I ensure proper fusion when welding the root pass?
To ensure proper fusion when welding the root pass, follow these guidelines:
- Cleanliness: Ensure that the joint surfaces are clean and free from any contaminants, such as rust, oil, or paint. Use appropriate cleaning methods, such as wire brushing or grinding, to remove any surface impurities.
- Fit-up: Properly align and fit the joint edges to ensure good contact and close fit between the base metal pieces. This helps facilitate heat transfer and proper fusion.
- Root opening and penetration: Control the root opening, which is the gap between the joint edges, to allow adequate penetration of the filler metal. The root opening should be within the specified range in the welding procedure.
- Welding technique: Use the appropriate welding technique for the process you are using. For example, in shielded metal arc welding (SMAW), use the proper electrode angle and maintain a consistent arc length. In gas tungsten arc welding (GTAW), control the torch angle and travel speed.
- Arc control: Maintain a stable arc throughout the root pass. Avoid excessive arc length, which can lead to insufficient penetration, or too short of an arc length, which can cause excessive heat and potential burn-through.
- Proper heat input: Control the heat input by adjusting the welding parameters such as amperage, voltage, and travel speed. Avoid excessive heat that can lead to distortion or overheating of the base metal.
- Backing or purging: Consider using backing bars, backing gas, or purging techniques to protect the root side of the weld and prevent oxidation or contamination. These methods help ensure proper fusion and a sound root pass.
- Visual inspection: Continuously monitor the weld pool and the fusion zone visually during the welding process. Ensure that the filler metal is fully melting and blending with the base metal.
- Post-weld inspection: After completing the root pass, inspect it for proper fusion. Look for indications of complete penetration, absence of cracks or lack of fusion, and a smooth transition between the weld and base metal.